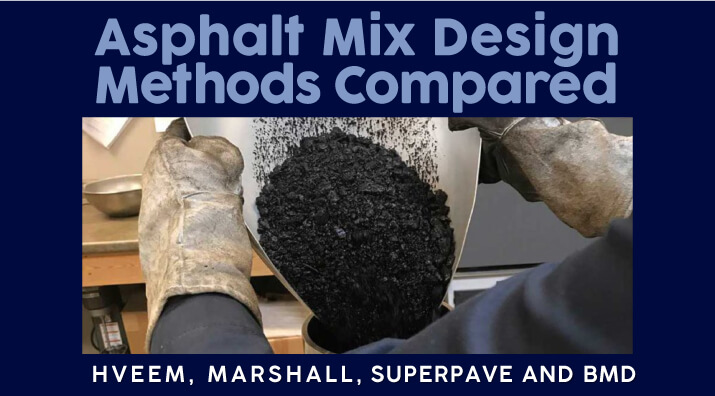
Like any construction material used in the built environment, our understanding of the properties and characteristics of asphalt and asphalt paving systems has evolved over time. The modern methods we use to design paving mixes continually improve as our body of knowledge matures.
The list of essential ingredients for hot mix asphalt is exceedingly short for a composite material with such complex characteristics: asphaltic cement and mineral aggregates. Modern, flexible pavements with different mix designs are simply variations in the properties and ratios of the essential ingredients and adjustments to temperatures, handling, and placement methods.
Not all asphalt mixtures serve the same purpose, even when used in the same pavement profile. Different points in the cross-section of a pavement call for other design considerations in the formulation of asphalt mixtures. A material with the strength and aggregate size to function as a base mixture may not be suitable for a surface course that requires durability and skid resistance to withstand long-term exposure to abrasion and environmental extremes.
What Works and What Doesn't?
Designing asphalt mixes in advance of production lets us forecast the behavior of a paving mixture during mixing, transport, lay-down, and throughout its lifecycle. Laboratory testing of trial batches allows us to fail quickly and on a small scale until a promising formulation is found and added to our knowledge base.
Closing the gap between laboratory results and real-world performance has long been the goal of researchers and practitioners. The popularity of different laboratory compaction, sample preparation, and design methods has waxed and waned as our understanding of material properties and the database of actual field performance increases. This article is an overview of past and present asphalt mix design methods and equipment, including Hveem, Marshall, Superpave, and Balanced Mix Design (BMD).
The Evolution of Asphalt Mix Design Methods
Historians trace the use of asphalt in road construction as far back as 650 BC in Babylonia. The Incan civilization used asphalt as a composite material to pave roads in Peru in the 1500s. The first "modern" asphalt pavement in the United States is thought to have been laid in New Jersey in 1870. According to the National Asphalt Paving Association (NAPA), more than 94% of the 2.6 million miles of paved roads in the U.S. today are surfaced with asphalt.
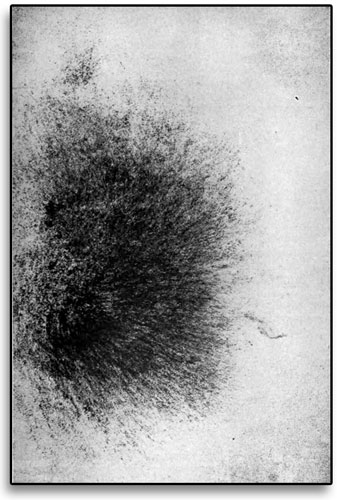
In the last few years of the 19th century, more modern notions of designing pavement mixes were evolving around the knowledgeable ideas and "recipes" put forward by materials engineers and experienced tradesmen, primarily based on empirical evidence. Quantitative or performance laboratory tests were unheard of. Clifford Richardson proposed one of the first qualitative tests in 1913. The "pat-paper test" provided a visual estimate of asphalt content by a sample's stain left on the paper.
Goals for All Mix Design Methods
When designing an asphalt paving mix to meet all the specified requirements of a project, all mix design methods share the same fundamental steps:
- Selection of Aggregates
Careful selection and blending of mineral aggregates are crucial for resisting permanent deformation failures in the asphalt. Particle size and gradation, angularity, toughness, and soundness are essential characteristics of a long-lasting pavement. - Selection of Asphalt Binder
Using a suitable grade of asphaltic cement or binder helps resist thermal and fatigue cracking, rutting, and shoving in pavements. Grading systems to classify asphalt binders use values determined by penetration, viscosity, or performance. - Penetration resistance to a weighted needle or cone of a specified diameter was an early type of test to classify asphalt cement. Penetrometers are still in widespread use.
- Viscosity grading came into use during the 1950s. The AC method is used to grade asphalt cement as supplied. The AR method was developed later to grade binders after aging that simulate the manufacturing and batching processes.
- The Superpave program of the 1990s introduced the performance grading (PG) system to classify asphalt binders. A series of new tests considered field performance, expected climate conditions, pavement temperatures, and aging to establish grading.
- Determination of the Optimum Binder Content
To establish the ideal proportion of binder in the job mix formula, the laboratory creates several trial mixes with different binder contents. The trial mixes are compacted into molds, and the molded specimens are tested for the desired characteristics.
Mix design methods differ in the how and why for each step.
Hveem Mix Design Method
Francis Hveem developed the Hveem mix design method in the early 1930s during his tenure as Resident Engineer for the California Division of Highways. He believed the best asphalt mix should have the highest binder content while still meeting the specified stability requirements.
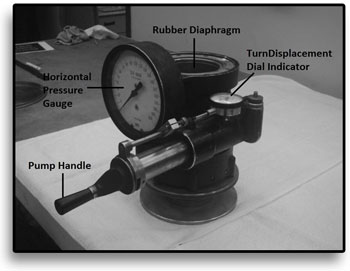
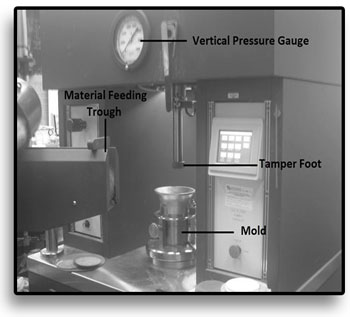
Hveem invented the Stabilometer loading device to measure the stability and cohesion of asphalt mixtures. After results showed that specimens prepared in the laboratory did not yield the same values as field samples, he developed the California Kneading Compactor to prepare more representative asphalt mix specimens for testing. The kneading compactor's action mimics the asphalt compaction by rollers during paving operations.
For the Hveem method, aggregate blends and binder types meeting the project requirements are selected. An initial asphalt binder content is then chosen from a predetermined list or estimated based on the ASTM D5148 (withdrawn) centrifuge kerosene equivalent (CKE) test.
A series of trial mixes with different binder contents are compacted in the California Kneading Compactor following ASTM D1561 / AASHTO T 247. The compacted specimens are tested with the Stabilometer using the ASTM D1560 / AASHTO T 246 standard test method. The optimum binder content is the highest asphalt content that still meets the specified stability, as determined through analysis of density and volumetric properties and stability test results. An ideal Hveem mix has about 4 percent air voids.
Marshall Mix Design Method
Bruce Marshall developed his asphalt mix design process in 1939 while working as an engineer with the Mississippi Highway Department. During World War II, the U.S. Army Corps of Engineers was looking for ways to fast-track the design and construction of airfield and runway pavements capable of handling the increased wheel loads of heavy aircraft and selected Marshall's process in 1943. The Marshall method met all their criteria, and the test equipment was easily integrated with existing California Bearing Ratio (CBR) practices for soil strength analysis.
The proven Marshall method produces strong, long-lasting pavements that resist damage from environmental forces and deformation from axle loads. Aggregates are selected and blended to meet size, gradation, angularity, and strength characteristics. Choices for asphalt binder types draw on local experience, prior performance, or, more recently, on Superpave Performance Grading (PG) ratings. Optimum binder contents are estimated, and trial mixes are produced in 0.5% content increments at, above, and below the estimates.
ASTM D6926 and AASHTO R 68 provide specific practices to prepare specimens for Marshall stability and flow testing. Trial asphalt mixes with carefully controlled proportions are blended in the laboratory and compacted into molds with manual or automatic drop hammers. The molded specimens, or "pills," are mounted in sample fixtures and tested for Marshall stability and flow properties in laboratory load frames following ASTM D6927 / AASHTO T 245 standard test methods. The specimens are also used to measure indirect tensile strength, fatigue, creep, density, and void analysis. Other test methods associated with the Marshall mix design method are listed in the chart below.
Test Description | ASTM Method | AASHTO Method |
Rice Test | D2041 | T 209 |
Bulk Density | D2726, D1188, D6752/T 166 | T 331 |
Marshall Compaction | D6926 | R 68 |
Marshall Stability & Flow | D6927, D5581 | T 245 |
Air Voids in Compacted Mixes | D3203 | T 269 |
Sample Thickness | D3549 | — |
Gilson offers a full range of laboratory equipment for the Marshall method design and testing process, and this previous Gilson blog article Marshall Test Method: Everything You Need to Know, discusses details of the procedures. The required testing equipment is straightforward, effective, and efficient for producing reliable and long-lasting pavements. The popular Marshall method is still in widespread use worldwide as it continues to be refined and adapted.
Superpave Mix Design
Since its origins in the mid-1980s, Superpave has dominated the landscape of asphalt pavement mix design. This federally funded program has upended the way pavement design is looked at, spurred research efforts, and fostered a variety of new test methods and testing equipment. This earlier Gilson blog article What is Superpave? Understanding Performance-Based Asphalt provides a close look at Superpave methods, tests, and testing equipment for asphalt binder, mineral aggregates, and analysis of mix designs.
Like the Hveem and Marshall methods, Superpave mixes are based on volumetric properties but factor in traffic loads and local climate considerations. Advanced viscosity, rheology, and aging tests are part of the Performance Grading (PG) used to classify asphalt binders. Selected aggregate shapes and gradations are blended for best performance. New and updated laboratory tests have improved the predictive modeling of pavement mixes by looking for properties that could aggravate cracking, rutting, and fatigue. The Superpave Gyratory Compactor (SGC) is a sample preparation method that uses hydraulic kneading pressure instead of drop-hammer impacts to prepare test specimens in sample molds. The instrumentation on the SGC also provides an analysis of the compactibility of asphalt mixes.
The Superpave design process begins with an examination of the project requirements. Temperature and other climatic conditions for the project region are noted, and pavement loadings expressed as equivalent single axle loads (ESALs) are factored into the mix design. After selecting binder type and aggregate gradation, several trial mixes are batched with binder contents at, above, and below the predicted optimum. After compaction in the SGC, theoretical maximum specific gravity (Rice test) and bulk specific gravity test results are used to calculate air void content and voids in mineral aggregates. This chart notes some test methods used to evaluate Superpave mix designs.
Test Description | ASTM Method | AASHTO Method | Testing Equipment |
Gyratory Compaction | D6925 | T 312 | Superpave Gyratory Compactors |
Theoretical Max Specific Gravity | — | T 209 | Asphalt Maximum Specific Gravity |
Asphalt Bulk Specific Gravity (SSD) | — | T 166 | Specific Gravity Accessories |
Asphalt Bulk Specific Gravity (Paraffin Coated) | — | T 275 | Specific Gravity Accessories |
Balanced Mix Design (BMD)
Governmental transportation agencies, pavement designers, and contractors acted on their shared concerns that simply combining ingredients in a prescribed manner was not producing pavements that met expectations for durability and service life. Balanced Mix Design (BMD) is a method that evaluates the suitability of asphalt mixes for specific applications based on performance and cost-effectiveness.
Traditional prescriptive mix designs draw from previous experience and the use of specified ingredients in prescribed volumes in the hope that all will perform well after placement. BMD allows realistic, fact-based predictions of pavement durability and crack resistance from data generated by laboratory performance tests. This earlier Gilson blog article Balanced Mix Design: A New Way Forward, discusses BMD in detail.
In 2018, a report to the National Cooperative Highway Research Program (NCHRP) entitled NCHRP Project 20-07/Task 406, the National Center for Asphalt Technology (NCAT) provided a context to develop BMD as a conventional approach to asphalt pavement design. In their later summary, Framework for Balanced Mix Design, NCAT provided drafts for two AASHTO provisional documents published in 2020:
AASHTO Standard Practice MP 46 is a guide for the selection and evaluation of materials and includes options for performance tests:
Distress Mode | Asphalt Performance Test | Test Method |
---|---|---|
Cracking | Disk-Shaped Compact Tension Test (DCT) | ASTM D7313 |
Illinois Flexibility Index Test (I-FIT) | AASHTO T 393 | |
Low-Temperature Semi-Circular Bend Test (SCB) | AASHTO T 394 | |
IDT Creep Compliance and Strength Test | AASHTO T 322 | |
Texas Overlay Test (OT) | TXDOT Tex-248-F | |
Direct Tension Cyclic Fatigue Test | AASHTO TP 107 AASHTO TP 133 | |
N flex Factor | AASHTO TP 141 | |
Flexural Bending Beam Fatigue Test | AASHTO T 321 | |
Semi-Circular Bend Test (Louisiana method) | LADOTD TR 330 ASTM D8044 | |
Indirect Tensile Asphalt Cracking Test (IDEAL-CT) | ASTM D8225 | |
Rutting | Hamburg Wheel Tracking Tester (HWTT) | AASHTO T 324 |
Asphalt Pavement Analyzer (APA) | AASHTO T 340 | |
High-Temperature Indirect Tension (HT-IDT) | ALDOT-458 ASTM D6931 | |
Rapid Shear Rutting Test (IDEAL-RT) | ASTM Work Item (WK 71466) | |
Flow Number Test (FN) | AASHTO T 378 | |
Stress Sweep Rutting (SSR) | AASHTO TP 134 | |
Moisture Damage | Tensile Strength Ratio (TSR) | AASHTO T 283 |
Abrasion Loss | Cantabro Abrasion Loss Test | AASHTO TP 108 |
AASHTO Standard Practice PP 105 illustrates different approaches to BMD mixes using flow charts:
Approach A and B:
Photo Credit: asphaltpavement.org
Approach C and D:
BMD methods optimize paving mixes to local conditions using fact-based results from selected performance tests. The test methods are straightforward, easily performed by any laboratory, and allow accurate long-term durability and crack resistance predictions under expected traffic loads and climatic conditions. The final job-mix formula (JMF) depends on the successful completion of these tests.
Balanced Mix Design Testing Equipment
As noted above, practical and uncomplicated tests that provide insight into lifetime pavement performance are at the heart of BMD. Gilson provides asphalt testing equipment for many Balanced Mix Design tests.
- BMD test specimens are prepared from Superpave Gyratory Compactor or Marshall Compaction specimens, sawed from compacted slabs, or cored from asphalt pavement.
- Several performance tests use unique sample fixtures to utilize Marshall Stability Apparatus or other Laboratory Load Frames. For various loading applications.
BMD Performance Test | Test Method | Sample Fixture |
Disk-Shaped Compact Tension Test (DCT) | ASTM D7313 | Loading Clevis & Displacement Gauge |
Indirect Tensile Asphalt Cracking Test (IDEAL-CT) | ASTM D8225 | Indirect Tensile Loading Fixture |
Illinois Flexibility Index Test (I-FIT) | AASHTO T 393 | Semi-Circular Bend (SCB) Test Fixture |
Low-Temperature Semi-Circular Bend Test (SCB) | AASHTO T 394 | Semi-Circular Bend (SCB) Test Fixture |
IDT Creep Compliance and Strength Test | AASHTO T 322 | Indirect Tensile Loading Fixture |
- Load displacement and data readout instrumentation are available to optimize load frames and fixtures for testing accuracy and efficiency.
- Asphalt Pavement Analyzers perform loaded-wheel tracking tests AASHTO T 324 and T 340 to assess asphalt resistance to rutting, fatigue, and moisture.
- The Los Angeles Abrasion Machine performs AASHTO TP 108, the Cantabro test for abrasion loss of asphalt mixes. The AASHTO provisional test originated in Spain.
- A unique Sample Preparation Saw is required for multiple semi-circular bend (SCB) or disc-shaped compact tension (DCT) test methods.
We hope this comparison of testing methods and equipment used for modern asphalt pavement mix designs has been helpful.