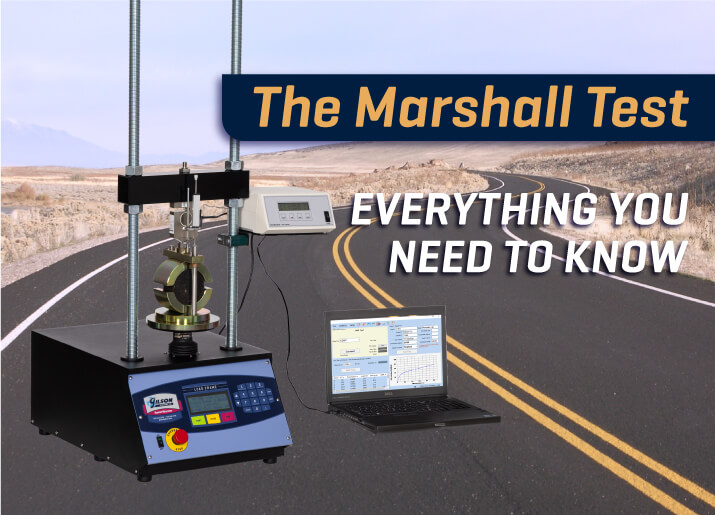
What is the Marshall Test?
The Marshall method of asphalt mix design is widely practiced in construction materials laboratories to select and proportion aggregate and asphalt materials for pavement construction. This holistic approach to asphalt pavement mix design involves the selection of mineral aggregate and binder materials, preparation of trial samples, load testing for strength and flow of materials, and lab tests of material properties. The focus is on determining an optimum asphalt content that will provide maximum power to the mix with minimum deformation from axle loads.
Marshall stability and flow test values, density, and air voids in the mix and the mineral aggregate are all used to evaluate trial mixtures of lab-mixed, lab-compacted (LMLC) asphalt mixtures. Marshall stability and flow tests can also monitor the production of the asphalt mixture using plant mix and laboratory-compacted (PMLC) samples.
Background and History
During World War II, there was an urgent need to quickly construct suitable airfields for large military aircraft with increasingly higher wheel loads. In 1943, the U.S. Army Corps of Engineers began evaluating several asphalt pavement mix design methods at their Waterways Experiment Station (WES) in Vicksburg, Mississippi. The Marshall Stability Method developed by Bruce Marshall at the Mississippi Highway Department in 1939 seemed to be the most promising after adding a procedure to measure deformation (flow). The Marshall method was recommended based on simplicity, rapid and effective test results, and the fact that some apparatus was compatible with equipment currently in use for the California Bearing Ratio (CBR) load test for subgrade soils. Because of its straightforward process and equipment, along with widespread use by the U.S. military, the method is used in some capacity by many state departments of transportation. It is the most widely used pavement design system in the world.
Marshall Stability Test: The Process
The Marshall process uses a series of laboratory tests and evaluation criteria for selecting materials and progressively narrows in on optimum mix design. A suitable mix will resist deformation from traffic loads and damage from climatic conditions and will have adequate skid resistance.
Note: Tests associated with Marshall mix design have procedures specified in several different ASTM and AASHTO test methods and many local and regional variations. The article's contents guide equipment and standard practices and are in no way intended to supersede requirements in any of these published test methods.
Aggregate selection begins with lab testing to measure the physical properties of aggregates. Abrasion resistance, soundness, durability, and particle shape all combine to ensure the aggregates are durable and contribute to the strength and resistance to deformation of the final asphalt mix. The chart below shows some typical laboratory tests performed to evaluate proposed aggregates. There are linked references for testing equipment and ASTM/AASHTO test methods.
Test Type | Test Method | Abrasion Resistance | Soundness | Toughness | Durability | Impact Resistance | Shape and Texture | Gradation | Specific Gravity |
---|---|---|---|---|---|---|---|---|---|
Los Angeles Abrasion | ASTM | ✓ | ✓ | ✓ | ✓ | ✓ | X | X | X |
Micro-Deval | ASTM | ✓ | X | ✓ | ✓ | X | X | X | X |
Sulfate Soundness | ASTM | X | ✓ | X | ✓ | X | X | X | X |
Durability Index | ASTM | ✓ | X | X | ✓ | X | X | X | |
Fine Agg Angularity | ASTM | X | X | X | X | X | ✓ | ✓ | X |
Sand Equivalent | ASTM | X | X | X | ✓ | X | X | ✓ | X |
Flat and Elongated | ASTM D4791 | X | X | X | X | X | ✓ | X | X |
Flakiness and Elongation | BS 812 | X | X | X | X | X | ✓ | X | X |
Particle Size Distribution | ASTM | X | X | X | X | X | X | ✓ | X |
Specific Gravity / Absorption | ASTM | X | X | X | X | X | X | X | ✓ |
Blending aggregates of different size fractions or shape characteristics is often performed to produce mixtures with greater densities, strengths, or handling properties.
Asphalt binder selection is not performed according to a specific procedure in the Marshall method. The Superpave Performance Grading (PG) binder system is often used, but the final selection may be based on experience, previous performance, or a local procedure. The PG system characterizes the suitability of an asphalt binder based on the expected climatic conditions and the aging conditions under which it is to be used. So, a binder selected for use in Florida would be different from the one used in Minnesota. PG binders are classified with two numbers representing the maximum and minimum pavement temperatures (in Celsius) at which they are suitable.

Sample preparation starts with an estimate of what the optimum binder content will be, based on experience and past performance. Several trial blends of aggregate and asphalt binder are prepared in laboratory-scale mixers with binder contents at, above, and below the estimated optimum in increments of 0.5%. Each trial mix must contain enough material to compact three specimens for stability and flow measurements, usually about 2.6lb (1.2kg) for each specimen. The ASTM D2041/ AASHTO T 209 theoretical maximum specific gravity, or Rice test, is performed to document the density characteristics of the design mix. Laboratory ovens are required to heat and condition aggregate and asphalt materials, compaction hammers, and molds.
Gilson Manual or Automatic Marshall Compactors perform safe and efficient sample compaction with 10lb (45.36kg) mass and 18in (457.2mm) drop height and stationary or rotating operation. The prepared and heated trial blends are compacted into Marshall compaction molds, each consisting of mold, collar, and base plate in 4in (101.6mm) or 6in (152.4mm) diameters. The number of blows required for specimen compaction is typically 35, 50, or 75, depending on anticipated traffic loads. The specified number of blows is applied to one side of the specimen, then the mold is reversed, and the same number is applied to the opposite side. The intact and compacted specimens are extracted from the mold with a sample ejector, and the bulk specific gravity is measured following ASTM D2726/AASHTO T 166
Stability and flow testing are described in test methods ASTM D6927/AASHTO T 245. The compacted asphalt specimen is conditioned in a water bath before being placed in a Marshall breaking head. The breaking head and specimen assembly are positioned in a Marshall stability tester outfitted with components to measure stability and flow during the test. Gilson Servo Control Load Frames precisely control rate of loading regardless of the applied load. This test predicts the performance of the trial mixes. Stability is the maximum strength of the mix when loaded at a rate of 2in (50.8mm) per minute. During the loading process, the plastic flow, or deformation of the specimen, is recorded in 0.01in (0.25mm) increments by a dial gauge or linear variable displacement transducer (LVDT). Data acquisition software is available to record, graph, calculate, and report Marshall test values automatically. ASTM D5581 can also be used with 6in (152mm) compacted specimens or pavement cores.
Characterization/measurement of density and voids are essential properties for a complete analysis of the proposed mix design. As noted above, specific gravity and density values are determined using the ASTM D2041/AASHTO T 209 theoretical method (Rice test) for the loose asphalt material and ASTM D2726/AASHTO T 166 to determine the bulk specific gravity of compacted specimens. There is also a need to describe various types of air void contents. Air void content in compacted mixtures consists of the small spaces between coated aggregate particles in a compacted mixture and is a test method defined in ASTM D3203/AASHTO T 269. Calculations determine two other void values.
- Voids in mineral aggregates (VMA) are defined as the void space between the aggregate particles in a compacted mixture. VMA is calculated based on the aggregate bulk specific gravity and is expressed as a percentage of the bulk volume of the compacted mixture.
The formula for calculating VMA is:
\[VMA = {100 - {GmbPs \over Gsb}}\]
Where:
VMA = Voids in mineral aggregate, in percent of bulk volume
Gsb = Bulk specific gravity of the aggregate
Gmb = Bulk specific gravity of compacted mix
Ps = aggregate, percent by total weight of mix
- Voids filled with asphalt (VFA) in a compacted paving mixture, consisting of that portion of the initial voids in the aggregate (VMA) filled with the non-absorbed asphalt.
The following equation can determine VFA:
\[VFA = {100({VMA - Pa \over VMA})}\]
Where:
VFA = voids in mineral aggregate, percent of bulk volume
Pa = air voids in the compacted mixture, percent of the total volume
The chart below references some ASTM and AASHTO standard test methods related to the Marshall mix design method, along with laboratory equipment required for the tests.
Test Type | Test Method | Maximum Specific Gravity and Density | Bulk Specific Gravity of Compacted Specimens | Asphalt Preparation and Compaction | Asphalt Stability and Flow | Percent Air Voids | Sample Height or Thickness |
---|---|---|---|---|---|---|---|
Rice Test | ✓ | X | X | X | X | X | |
Bulk Density | X | ✓ | X | X | X | X | |
Marshall Compaction | ASTM D6926 AASHTO R 68 | X | X | ✓ | ✓ | X | X |
Stability and Flow | ASTM D6927 D5581 AASHTO T 245 | X | X | ✓ | ✓ | X | X |
Air Voids in Compacted Mixes | ASTM D3203 AASHTO T 269 | X | X | X | X | ✓ | X |
Sample Thickness | ASTM D3549 | X | X | X | X | X | ✓ |
We hope this blog has given you a better understanding of the Marshall asphalt mix design method and some of the associated test standards and lab equipment. Visit our Marshall Testing Equipment for a complete list.