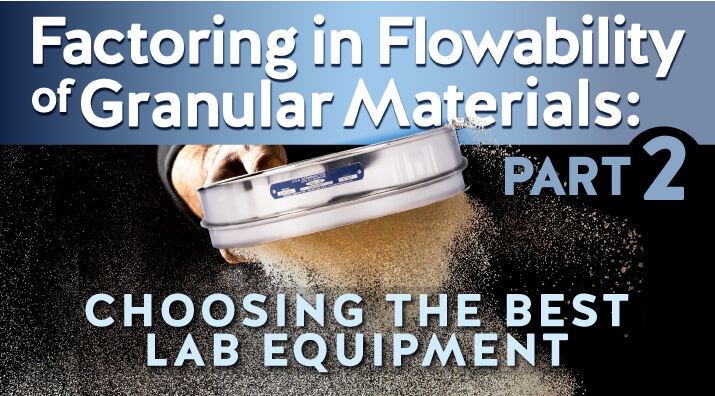
Test methods for dry granular materials must be built around the flowability of the material. No sampling, sizing, or handling method can be performed accurately or efficiently if it does not work in harmony with the material's flow properties.
Flowable powders and granular materials have many characteristics that govern their movement and flow while being handled and tested. The selection of the most effective laboratory equipment for granular material is dictated by the nature and physical properties of the material and its condition during processing.
Sieving for Size Analysis
Part 1 of this series explored issues and solutions for the flowability of granular materials and powders when preparing representative samples for testing. Not surprisingly, many of those issues persist throughout subsequent stages of particle sizing or other testing. This second and final installment looks at strategies and equipment to enhance the flow characteristics of particles for sieving and sizing tests.
Flow characteristics are revealed when physical forces are imposed on granular materials to separate the size fractions. Fine, lightweight particles may fly away or stick to oppositely charged surfaces on testing equipment. Large particles with flat and elongated shapes or angular surfaces may catch against each other, impeding or stopping flow through the mesh openings of sieves. The repetitive actions of manual or mechanical sieving agitation and tapping may fracture or degrade particles, changing their flow characteristics and dimensions.
Material Property | Improved Flow | Reduced Flow | Solutions for Low Flowability |
---|---|---|---|
Shape & Texture | Smooth, spherical particles flow easily over or around similar shapes | Flat and elongated particles or those with rough, angular textures snag other particles, restricting flow, and blinding mesh openings |
|
Relative Density (Specific Gravity) | Dense materials respond more quickly to gravity, overcoming constraints and increasing flow rates | Low-density particles are more sensitive to the effects of moisture and static attraction and are less responsive to gravity, inhibiting flow |
|
Particle Size | Coarse particles resist cohesive and attractive forces, allowing them to move more independently | Fine particles and powders often form cohesive bonds, reducing flowability |
|
Moisture Content or Relative Humidity | Surface moisture in coarse materials may lubricate particles and promote flow | Humidity or moisture causes fine materials to agglomerate, impeding flow and affecting particle size tests |
|
Electrostatic Attraction | Controlled humidity or electrical grounding may help control issues with static attraction | Fine, dry, lightweight particles may cling to sampling and testing equipment surfaces |
|
Accurate, repeatable, and efficient particle sizing with test sieves relies on maximizing flowability and applying agitation to increase the possibilities of a particle passing through a mesh opening. Whether agitation is applied manually or through a sieve shaker, the optimum action for separation repeatedly lifts particles off of the mesh surface and allows them to land in a different position, assuring each particle is tried against multiple openings in different orientations. The addition of an abrupt bumping or tapping action on the test sieve significantly improves the passage of near-size particles through the sieve apertures.
Test Sieves
With a few exceptions, the flow properties of materials are influenced less by the type of sieve than by the agitation action applied during the test. Test sieve types should be selected based on the application, the level of accuracy needed, and the requirements specified in the standard test method.
Test sieves in a variety of configurations and types are available from Gilson. This article focuses on conventional round sieves mounted with woven wire or electroformed mesh. Both types of mesh have their place with advantages and disadvantages to be considered.
- Woven Wire mesh in test sieves is rugged and cost-effective. These commonplace sieves are widely used and frequently specified. The weaving process produces variations in the size and shape of openings, but the tolerances are well understood and reflected in the specifications.
- Electroformed mesh is flat and has square openings with precise dimensional tolerances. These sieves feature high accuracy, but the cost is also high, and the fine mesh sizes are delicate and easily damaged. Electroformed mesh is generally reserved for fine powders when superior accuracy is required.
Sieve Shakers
Sieve shakers enhance all aspects of particle sizing tests compared to manual agitation. For any granular material, they increase accuracy, repeatability, and efficiency by removing human error and other inconsistencies. When comparing similar materials or replicating grain sizes for production, they allow meaningful correlations between testing locations. The sieve shaker must be matched to the material characteristics To maximize the benefits of these features.
A sieve shaker with an action that enhances the flowability properties of a given material is the best choice for accurate and efficient particle sizing. A powerful, high-amplitude model with aggressive tapping might be just the ticket for coarse, heavy construction aggregates but would quickly degrade a fine, lightweight powder and lose it into the air as dust.
A shaker that complements the flow characteristics of a material increases sieving efficiency. During agitation, particles are in motion and scraping against one another, causing attrition and damage. There must be enough agitation time to fully separate the fractions, but not so much that it damages the sample. Soft, brittle, and fragile materials can be ground down or fractured, skewing test results for the particle size analysis and subsequent lab tests for that sample.
Here are some basic characterizations for different types of sieve shakers.
- Mechanical Sieve Shakers have an electric motor connected to a pulley or gearbox to provide a repetitive action that agitates the sieve stack. Mechanical sieve shakers give reliable performance and are a good choice for easy-to-sieve materials between 50mm and 20µm (2in and No.635). Models can be further classified according to the type of action they generate but generally do not have much adjustability to fine-tune their agitation for different materials.
- Circular sieve shakers move on a flat, circular plane, evenly distributing material across the mesh surfaces to fall through random openings. Including a tapping feature on premium models allows a size range of as much as 50mm to 20µm (2in to No.635) and improves passing efficiency for near-size particles. Basic units without tapping are effective on free-flowing materials between 4.75mm and 150µm (No. 4 and No. 100).
- Rotary Sifters rotate an assembled sieve stack resting at an angle as the material continuously reorients on each sieve. Multiple tappers contact each sieve to improve particle passing efficiency. The entire mechanism is enclosed in a cabinet for safe operation and to minimize dust and noise. Rotary Sifters are well suited for moderately dense, free-flowing materials from 4.75mm to 20µm (No. 4 to No. 635).
- Orbital sieve shakers are a cost-effective option for sieving free-flowing materials from No.4 4.75mm to 75µm (No. 4 to No.200). For these units, the base of the sieve stack moves in an orbital motion and is suspended from a single point at the top. Particles roll over the surface of the sieve mesh until they fall through an opening. The orbital action is intended to reproduce the motions of hand sieving, and some models introduce a bumping feature during oscillation to assist passage.
- Vibratory Sieve Shakers agitate materials using electromagnetic energy. Vibrations lift particles off the mesh surface, forming a fluid bed of material flowing across the sieve. The particles are continuously reoriented to be tried against different openings. Models with advanced designs feature adjustable amplitude and frequency to match shaker performance with material flowability, selectable tapping, or a programmable vibration pause that mimics tapping action. Vibratory shakers are ideal for samples from 2mm to 20µm (No. 10 to No.635). Power input controls increase range, optimize efficiency, and protect fragile samples from attrition.
- Sonic Sifters use 60 pulses per second of acoustically generated energy to agitate samples in an active enclosed air column formed by the sieve stack. These units excel at precise separations of small samples of fine powders to 5µm or finer and are used frequently with Precision Electroformed Sieves.
Sonic sifters are much more customizable than other sieve shakers and include programmable energy input, ramp/dwell levels, testing profiles, and selectable horizontal or vertical tapping to leverage the flow characteristics of "difficult" materials.
- Air Jet Sieve Analyzers direct a gentle stream of air from a rotating nozzle upwards through the bottom of a test sieve to fluidize and disperse the sample and reorient the particles. The process only retains coarse material on one sieve at a time. Particles passing the sieve openings are drawn away by vacuum to be retained in a cyclone collector or discarded. The Air Jet is in its element when separating single fractions of fine, fragile, and low-density materials down to 20µm (No. 635) size. Still, the creation of a multi-point size distribution curve requires multiple cycles. Advanced data acquisition and transfer options include printer ports, compatible balances, and networked information management systems.
Other Strategies to Defeat Poor Flowability
- Wet Sieving
Sieving is ordinarily performed with dry samples. The free-flowing properties of most granular materials are best when they are dry. The test methods are simple, and the equipment is relatively low-cost. Still, some materials have characteristics that resist accurate separation in a dry state. Electrostatic attraction or humidity conditions may cause some fine powders to clump together. Granular soils with a fines content and coal, marine sediments, slurries, and other non-soluble material are often easier to separate in wet conditions, as discussed in this Gilson blog article, Wet Sieving: A Practical Guide.There are two approaches to using water in particle sizing operations:
- Washing to remove finer or cohesive material from a bulk sample is a straightforward operation. The objective could be determining the percentage of fines or simply making the material easier to sieve by eliminating the cohesive fraction. In this process, one or two wet-wash sieves are manually agitated in a stream of flowing water. Fines become suspended in the water and removed when the water is decanted. Aggregate Washers automate the procedure using a rotating tilted drum allowing wash water to spill into a sieve.
- Wet Sieving for particle sizing involves a controlled distribution and drainage of water through a stack of sieves mounted on a sieve shaker. The apparatus required ranges from adaptive modifications to ordinary sieve shakers and test sieves to a self-contained system with vibration control, filtration to recover fines, and water distribution and recovery. Accessories are available to craft a wet sieving system to suit specific applications.
- Sieving Flow Agent
Fine powders with a tendency to agglomerate can still be accurately tested with sieves by using a Sieving Flow Agent. Combining a small amount of this very fine silicone dioxide powder into a sample eliminates clumping caused by electrostatic forces and high humidity. The material has a very low bulk density, so it has little to no effect on sieving results. - Sieving Aids
Where the objective of separating size fractions is production rather than analysis, sieving aids are often used to boost throughput and enhance productivity. These devices include objects of various sizes, shapes, and materials placed on the sieves along with the sample. During agitation, the aids break up agglomerations and force the passage of particles through the sieves. For gradation and particle size testing, Gilson does not recommend using these sieve aids since they may alter the size, shape, and surface area of sample particles and damage the sieve mesh.
We hope this article has helped you understand the impact of material flowability on particle size testing and the selection of testing equipment.