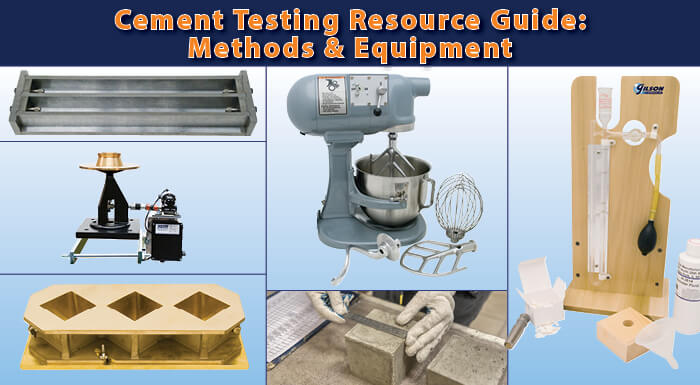

If we’re going to discuss cement testing, we should be clear about what we mean by “cement.” A single definition is hard to pin down, and cement can’t be characterized as just one material.
What is Cement?
In a general definition, hydraulic cement is a powder that when mixed with water, undergoes a chemical reaction called hydration. The cement paste hardens and gains strength as it cures over time. Portland cement is the most common type of hydraulic cement and forms the basis of most cementitious materials used for concrete, mortar, and grout.
What is the difference between Mortar and Grout?
- Mortar is a compound made with hydraulic cement, sand, water, and lime, used to bond brick or block masonry units together. Mortar consistency must be thick enough to stay on the masonry surfaces during placement and maintain correct joint thickness under load until cured.
- Grout often has a similar composition to mortar but can be made with many different ingredients that control its consistency and flow. Grout has a higher viscosity, allowing it to flow into the voids and recesses between structural surfaces or preplaced aggregate.
History of Cement
The history of cement is complex and anything but linear. We know that ancient Egyptians used super-heated (calcined) gypsum as cement long before Greeks and Romans combined calcined limestone and sand to create a different version. Romans were the first to discover that adding finely-ground volcanic pozzolanic materials would enhance the strength of their concrete mixes.
Who Invented Cement?
The development of modern cements is rooted in the United Kingdom beginning in the 1750s. Many individuals, ranging from engineers and researchers to brick masons and tinkerers, slowly developed and improved formulations over the next century. Their compounds were varied combinations of heated lime or ground limestone mixed with clays, shales, slates, or chalk. Between 1824 and 1853, Joseph Aspdin of Leeds and his son William developed the most successful formulation and process. Equally as crucial as refinements in chemical composition were the introduction in the 1860s of rotary kilns in the United States and Germany. These new devices allowed virtually continuous production of a much higher-grade cement product.
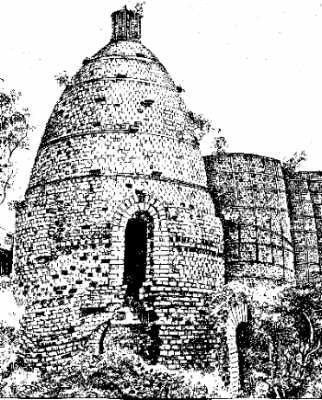
Aspdin's Beehive Kiln, Photo Credit: Dartford museum
How Is Cement Made?
The manufacture of hydraulic cements begins by compounding carefully controlled portions of limestone, shale, clay, and iron ore. Blended cements may also add slags or pozzolan materials. A sloped rotary kiln, which can be 10 to 15 feet in diameter and up to 300 feet long, heats the raw compound. Materials are heated to between 2,700° and 3,000°F (1,480° to 1,600°C) while rotating along toward the lower end. The calcining process creates new chemical compounds and results in marble-sized pellets called “clinker,” which are then finely ground to produce the cement powder. The producer may add Gypsum or lime during grinding.
The 3 Major Cement Specifications And Their Cement Types
1. ASTM C150/AASHTO M 85 is a prescriptive specification and lists both the chemical composition required and the physical tests needed to characterize the material. ASTM C150 defines ten types of Portland cement, based on five basic formulations:
- Type I: A general-purpose cement, used mostly in the production of Portland cement concrete.
- Type II: Cement with moderate sulfate resistance for concrete in direct contact with soils or groundwater. Most cement sold in North America will meet either Type I or Type II specifications.
The fineness of Type II cement can be manipulated during the grinding phase to reduce the heat of hydration, desirable in mass pours such as dams or bridge abutments. A material with larger individual particles has reduced surface area and, subsequently, a slower rate of hydration. Custom grinding adds both Type ll(MH) and Type ll(MH)A cements to the list.
- Type III: Similar to Type I, but ground to a smaller particle size during production. Develops strength more quickly and is known as “high-early” cement.
- Type IV: The lower heat of hydration and a slower rate of strength development controls internal temperatures on mass pours. Blended cements that are less expensive and more reliable have mostly replaced Type IV cement.
- Type V: This type resists sulfate attack in applications where sulfate soils and groundwater would cause permanent damage to ordinary cement. Cements blended with blast furnace slag and fly-ash are more effective and less expensive to produce than Type V cement.
Note: Air entraining compounds added to Types I, II, and III during production produces Types IA, IIA, and IIIA cements. Separate air-entraining admixtures dosed directly into ready mix concrete batches have mostly replaced these modified cement types.
2. ASTM C595/AASHTO M 240 is a prescriptive specification but covers blended hydraulic cements. It details the composition and tests required for blended hydraulic cements that contain Portland cement as the main ingredient. Additional materials are blended in to reduce the cost, alter set times, and modifiy the characteristics of plain Portland cement. These blends enhance workability, prevent alkali/aggregate reactions, reduce water demand, and more.
Blends commonly include slags from blast furnace operations or pozzolans like coal ash and silica fume from coal-fired electricity production. Using slag from steel production and coal ash from coal-fired electrical plants reduces the environmental impact of these waste materials. There are four main categories of blended hydraulic cements:
- Type IS: Portland-Slag Cement contains 25% to 70% blast furnace slag products by weight.
- Type IP: Portland-Pozzolan cement Includes coal ash and silica fume waste materials.
- Type IL: Portland-Limestone Cement has added calcium carbonate and gypsum and reduces the amount of carbon dioxide released during production.
- Type IT: Ternary Blended cements add two types of additional cement materials instead of just one to basic Portland cement to produce desired qualities.
Note: Letter suffixes designate additional features and ingredients, as noted in the specification. For example, Type IP(MS) is a Portland-pozzolan cement with moderate sulfate resistance. (HS) indicates high sulfate resistance, and (MH) is for moderate heat of hydration.
3. ASTM C1157 is also a performance-based specification for hydraulic cements. It places no restrictions on the chemical composition of the materials, and only requires adequate performance in a series of physical tests.
ASTM C1157 specification categorizes hydraulic cements by their performance attributes instead of their content. There are no requirements for chemical composition. Type designations for these cements are straightforward:
- Type GU: General Use, when particular types are not required
- Type HE: High Early-Strength
- Type MS: Moderate Sulfate Resistance
- Type HS: High Sulfate Resistance
- Type MH: Moderate Heat of Hydration
- Type LH: Low Heat of Hydration
Cement Test Methods & Testing Equipment List
Each of the three major specifications for hydraulic cements references some or all of the listed equipment. Our list below shows the most common testing equipment used for the physical testing of cement. Also, their use is incorporated into other ASTM/AASHTO test methods for cement as noted.
Compressive Strength
ASTM C109/AASHTO T 106
Compressive Strength of Hydraulic Cement Mortars
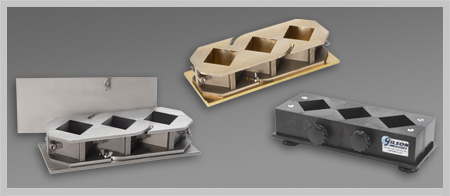
Cube Molds for Cement Testing
Also referenced in ASTM C87, C91, C141, C311, C472, C579, C942; AASHTO R 64
Fineness of Cement
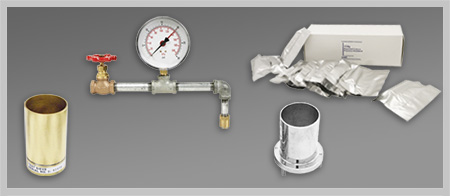
ASTM C430/AASHTO T 192
The Fineness of Hydraulic Cement by the 45µm (No. 325) sieve
Cement Fineness Apparatus
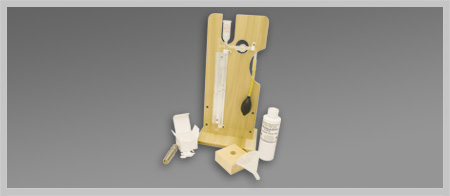
ASTM C204/AASHTO T 153
The Fineness of Hydraulic Cement by Air Permeability Apparatus
Blaine Air Permeability Apparatus
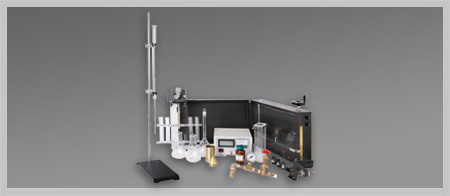
ASTM C115/AASHTO T 98
The fineness of Portland Cement by the Turbidimeter
Wagner Turbidimeter
Consistency Test of Cement
ASTM C230/AASHTO M 152
Flow Table for Use in Tests of Hydraulic Cement
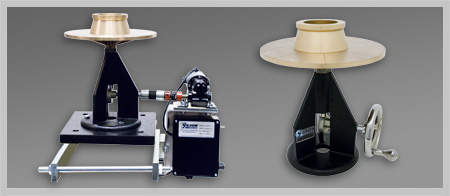
Flow Table Test Apparatus
Also referenced in ASTM C87, C109, C110, C185, C348, C860; AASHTO T 71, T 106, T 137
Setting Time of Cement
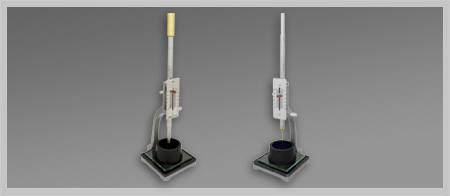
ASTM C191/AASHTO T 131
Time of Setting of Hydraulic Cement by Vicat Needle
Vicat Apparatus
Also referenced in ASTM C91, C141, C187, C308, C451; AASHTO T 129,
T 186
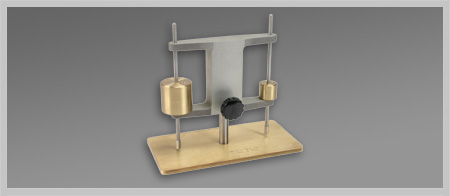
ASTM C266/AASHTO T 154
Time of Setting of Hydraulic Cement by Gilmore Needles
Gilmore Needle Apparatus
Length Change/Soundness of Cement
ASTM C151/AASHTO T 107
Autoclave Expansion of Portland Cement
Air Content of Cement
ASTM C185/AASHTO T 137
Air Content of Hydraulic Cement Mortar
Specific Gravity/Density of Cement
ASTM C188
The density of Hydraulic Cement
References and Useful Links
- Portland Cement Association offers an explanation of cement types, applications, and nomenclature in this article, and thorough reviews and characteristics in two popular publications:
- Design and Control of Concrete Mixtures
- Effects of Cement Characteristics on Concrete Properties
- Significance of Tests and Properties of Concrete and Concrete-Making Materials, ASTM Publication STP169D, Lamond JF, Pielert JH, 2006. The chapters in Part V, Other Concrete Making Materials, are particularly useful for cement testing.
We hope this blog post has helped you select the right cement testing equipment needed for your lab. Please contact the testing experts at Gilson to discuss your application.
Testing Resources
Standard Test Methods, Specifications, and Practices
Individual test methods and specifications referenced in our product descriptions, blog articles, and videos are available for review or purchase from the professional organizations noted.
- ASTM International (American Society for Testing and Materials)
- AASHTO (American Association of State Highway and Transportation Officials)
- ACI (American Concrete Institute)
- State DOTs (Departments of Transportation)
- ISO (International Organization for Standardization)
- BS (British Standards)
- EN (European Standards)