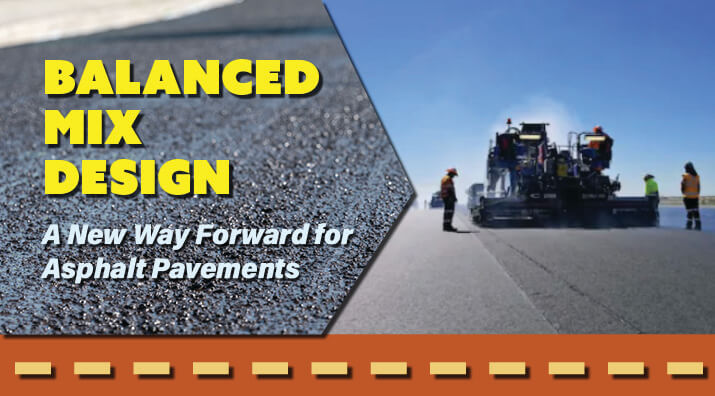
Since its inception, asphalt mix design has followed prescriptive, volumetric approaches. Ingredients are selected and then mixed in a prescribed manner to arrive at an asphalt paving material that meets specifications. Acceptance has been determined based on air voids, voids in mineral aggregates (VMA), and voids filled with asphalt (VFA). But some of the effects of reclaimed and recycled asphalt materials may not be reflected in these volumetric properties. Until recently, other factors like temperature profiles and the local environment were only regarded empirically based on the knowledge and experience of designers or specifiers.
Many stakeholders in industry and government have concluded that simply combining specified ingredients in prescribed volumes is a poor predictor of how those ingredients will interact in service and the pavement's long-term performance. Cracking and rutting have continued to be significant issues affecting pavement durability and longevity. Robert Lee, TXDOT Director of Flexible Pavements, stated: "Let's stop using the recipe to determine if the cake is good."
Taking Up the Challenge
In 2015, a Federal Highway Administration (FHWA) expert task group on asphalt mixtures examined improved methods to design mixes for asphalt pavement. The Task Force formed from this group defined balanced mix designs (BMD) as "...asphalt mix design using performance tests on appropriately conditioned specimens that address multiple modes of distress taking into consideration mix aging, traffic, climate, and location within the pavement structure."
The BMD Task Force recommended that each asphalt mix design undergo two or more performance-type tests to evaluate common forms of distress, such as rutting and cracking. They also proposed different approaches for pavement designers to administer the BMD process.
Steps Toward Change
Performance tests must be selected to reliably predict how a mix withstands particular types of distress in the local environment. The test methods must be simple and easily performed by any laboratory. Rather than select material proportions based on past experience, material costs, or specification limits, BMD methods optimize mixes for targeted local distress modes using evidence-based test results. Only after the successful completion of these performance tests would a particular mix be approved for use as a job-mix formula (JMF).
The National Cooperative Highway Research Program researched goals for implementing BMD and completed NCHRP Project 20-07/Task 406 in 2018. A survey performed for this study by the National Center for Asphalt Technology (NCAT) found that Iowa, Illinois, Louisiana, New Jersey, Texas, and California are currently employing different aspects of BMD methods. Other states have incorporated performance testing into their acceptance criteria in some form for only a single mode of distress. The majority of respondents were open to initiating trial studies to evaluate more BMD methods and establish simple and straightforward procedures for the balanced mix design process.
In their Framework for Balanced Mix Design, NCAT summarized their report to NCHRP, identified knowledge gaps needing continued research, and initiated drafts for two AASHTO provisional documents published in 2020.
- AASHTO Standard Practice MP 46 is used to select and evaluate materials for asphalt BMDs, listing options for performance tests and summaries of test criteria used by state highway agencies.
- Standard Practice PP 105 is a guide governing the development of asphalt mixtures using BMD practices. These recommended approaches are summarized below.
Approach A:
Photo Credit: asphaltpavement.org
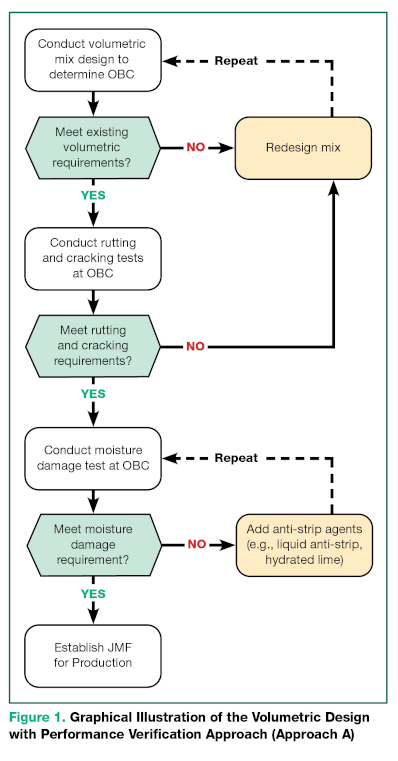
Approach B:
Photo Credit: asphaltpavement.org
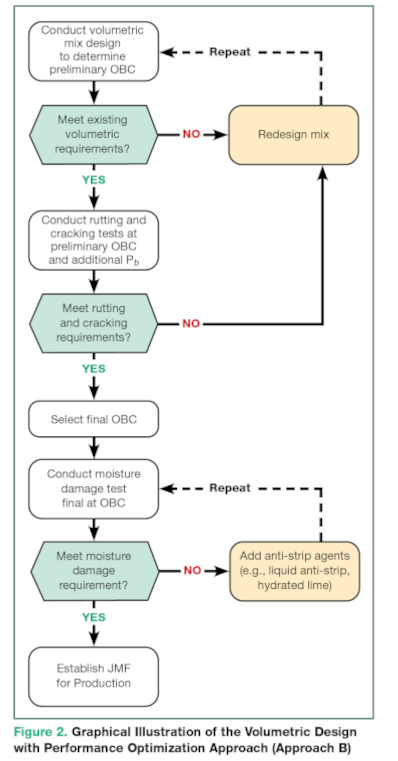
Approach C:
Photo Credit: asphaltpavement.org
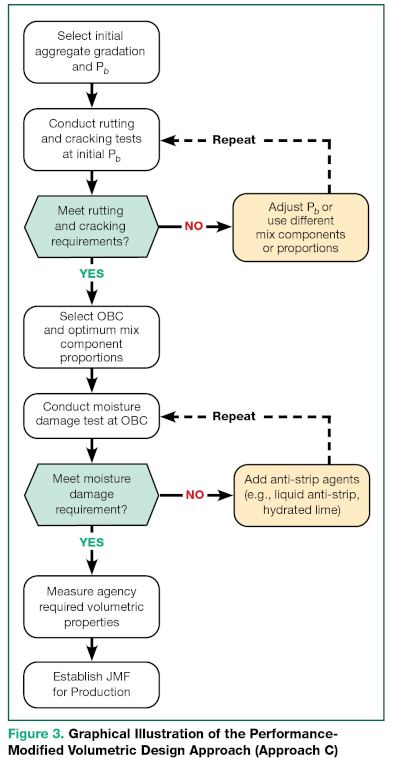
Approach D:
Photo Credit: asphaltpavement.org
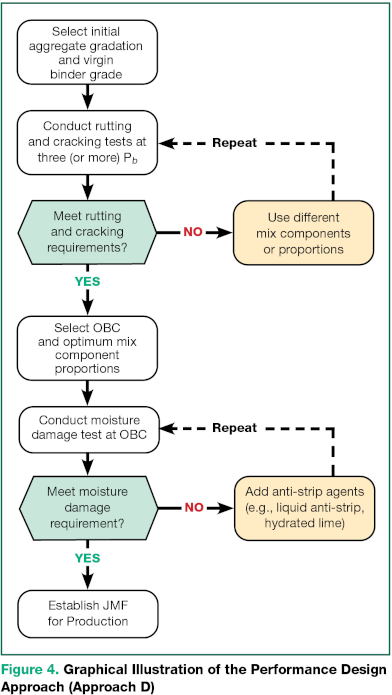
Selecting From the Menu of Performance Tests
Many elements of BMD are not new. Good design practices are still crucial to good pavements, and reliable tests still produce reliable results. What's different is the selection and significance of the performance tests and how the results apply to the acceptance of mixes.
Testing Equipment for Balanced Mix Design Performance Tests
One of the objectives in developing a balanced mix design is that the performance tests should be simple enough to be completed in any construction materials lab. Straightforward test methods using affordable laboratory testing equipment ensure effective testing is performed efficiently.
Since the selection of appropriate performance tests varies depending on traffic loads, climate, and placement within the pavement structure, versatile testing equipment that easily adapts to perform multiple tests has real value.
Follow the links below to view recommended Gilson testing equipment for BMD performance tests.
- BMD performance test samples are obtained or prepared from a variety of sources. Specimens are often prepared in a Superpave gyratory compactor, sawed from prepared slabs using masonry saws, or cored from asphalt pavement (see asphalt coring equipment).
- BMD test methods like IDEAL-CT, I-FIT, and SCB require stabilization of specimen temperatures prior to testing. A sample conditioning chamber holds up to six 6in (152mm) or sixteen 4in (102mm) diameter specimens, depending on height, and precisely controls chamber temperatures to ±0.5°C.
- Several BMD tests that assess asphalt cracking or strength properties use laboratory load frames suitable designed for Marshall stability testing. Special sample fixtures are available to adapt the load frames for BMD tests. Specified load and displacement or data readout instruments may be required for particular test methods.
- Marshall Stability Load Frames have a fixed strain rate of 2in (50.8mm) per minute and total capacities of 10,000lbf (44.5kN) or 20,000lbf (89kN). The crosshead adjusts to accept test fixtures up to 19.5in (495mm) high.
- Servo Control Load Frame has a variable strain rate from 0.00001–2in/min (0.0001–50.8mm/min), suitable for asphalt specimens and many geotechnical soil tests. Frame capacities are 10,000 or 20,000lbf (44.5 or 88.9kN).
BMD Performance Test | Test Method | Sample Fixture |
Disc-Shaped Compact Tension Test (DCT) | ASTM D7313 | Loading Clevis and Displacement Gauge |
Indirect Tensile Asphalt Cracking Test (IDEAL-CT) | ASTM D8225 | Indirect Tensile Loading Fixture |
Illinois Flexibility Index Test (I-FIT) | AASHTO T 393 | Semi-Circular Bend (SCB) Test Fixture |
Low-Temperature Semi-Circular Bend Test (SCB) | AASHTO T 394 | Semi-Circular Bend (SCB) Test Fixture |
Indirect Tensile (IDT) Creep Compliance and Strength Test | AASHTO T 322 | Indirect Tensile Loading Fixture |
- The Asphalt Pavement Analyzer models perform both AASHTO T 324 and T 340 loaded-wheel tracking tests to assess asphalt mixes' rutting, fatigue, and moisture susceptibility characteristics. The versatile APA models can be adapted to perform a variety of tests in dry or submerged environments.
- The Los Angeles Abrasion Machine is used to perform AASHTO TP 108, known as the Cantabro test, to determine abrasion loss of asphalt mixes. The test originated in Spain and has been adopted by AASHTO as a provisional test method.
Useful Resources for Balanced Mix Design:
- National Asphalt Paving Association (NAPA),
- National Center for Asphalt Technology (NCAT)
We hope this article has helped you understand the balanced mix design concept for asphalt pavements. For more information, visit our asphalt testing equipment page, or please contact our testing experts for questions or help with your application.
Testing Resources
Standard Test Methods, Specifications, and Practices
Individual test methods and specifications referenced in our product descriptions, blog articles, and videos are available for review or purchase from the professional organizations noted.
- ASTM International (American Society for Testing and Materials)
- AASHTO (American Association of State Highway and Transportation Officials)
- ACI (American Concrete Institute)
- State DOTs (Departments of Transportation)
- ISO (International Organization for Standardization)
- BS (British Standards)
- EN (European Standards)