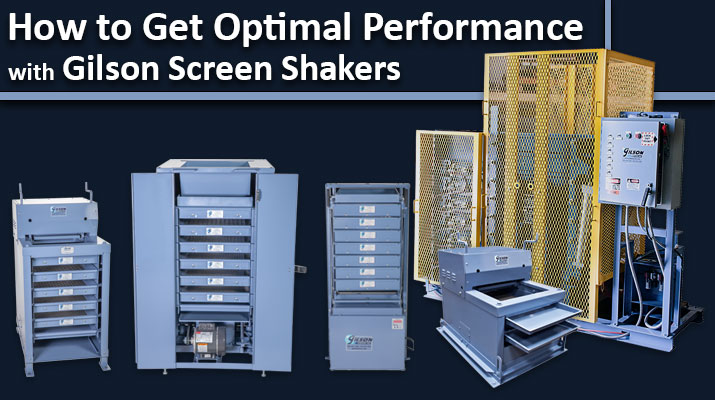
Today’s blog post is all about maintenance, Installation, care, and upkeep of each model will be covered, as well as some basic topics that apply to all the testing screens.
Housekeeping
Aggregate testing is a dirty business, and if your testing screen still has that showroom shine, you’re not using it enough. Keeping your laboratory screening equipment relatively clean doesn’t take much effort and has some real benefits. Allowing dirt and dust to build up causes problems with the efficiency and function of testing screens and will eventually affect test results
After each day of use, take a minute and brush or vacuum dust off the unit. More than just cleaning up, paying attention to this chore can also yield clues about the condition and performance of your machine.
- Look for damaged or missing parts as you clean. Catching them before the next use could prevent further damage.
- Seeing more dust or fines than usual may indicate damaged or improperly secured screen trays.
- On units with hydraulic clamping, look for traces of oil that might indicate a leak.
Hydraulic Systems
The hydraulic clamping system of Test-Master® and most Testing Screen models are the most efficient and secure way to clamp screen trays in place for testing. This system is a proven performer, but optimum performance requires regular maintenance.
- Hydraulic pumps are rugged proprietary units made from solid aluminum castings and quality components. They have a long service life, even with daily use, and can then be rebuilt inexpensively with available kits. Minor repairs are simple, often just replacing common O-ring seals. For day-to-day operations, they only need to be monitored for minor leaks at connections and topped-off with hydraulic fluid.
- Hydraulic Cylinder Assemblies are activated by the hydraulic pump to tighten or release clamping pressure on the screen trays. On Testing Screens, they attach to the clamp rods at the top of the machine. For Test-Master models, are located at the bottom of the frame and act on the separator guide pins to secure the trays.
Screen Trays
Screen Trays for Test-Master and Testing Screen models are interchangeable and will also fit the Continuous-Flow unit in place of Inclined Screen Trays. Porta-Screen Trays have a similar design but are smaller.
- Wire Cloth is the most crucial component in any particle sizing test. The mesh openings must be accurate and undamaged to produce accurate results. Screen tray design allows quick and easy replacement of wire cloth, and pre-cut replacements are available in every opening size of both ASTM and ISO cloth.
- Screen Tray Flanges must be straight and undamaged for proper installation into the screen shakers. They are relatively easy to repair, but a lot easier to use if not damaged in the first place. Sensible handling during use and proper storage between uses will prevent almost all damage and make the trays much easier to handle.
- Screen Tray Verification is a Gilson service to certify that opening sizes and wire diameters of the wire cloth meet ASTM or ISO calibration or inspection grade requirements.
Maintenance by Model
Each type of testing screen is unique and has different requirements to keep them performing in top condition. The following information is an overview of the basic requirements for each model. The operating manuals contain detailed installation, operating, and maintenance instructions, as well as parts lists and diagrams. Consult the latest editions linked below for complete maintenance and repair information.
Gilson Testing Screens
Models TS-1 and TS-3 Testing Screens have many similarities, and the maintenance requirements detailed in the operating manual are essentially the same. The older TS-2 model with a manual crank clamping system is no longer in production, but many units are still in operation and Gilson continues to stock repair parts. The new TS-4 Silent Testing Screen shares the hydraulic clamping system and drive mechanism of the original models but has a separate manual. The simple design and rugged construction of these units mean upkeep and repairs are straightforward.
- Installation: Testing Screens require bolting in a permanent location to a rigid floor system, preferably concrete.
- Clamping Systems: Testing Screens use clamp rods with either a hydraulically (described above) or a manually operated mechanism (no longer in production) to secure the screen trays during agitation. During operation, the clamp rods move vertically through upper and lower guide bearings. Predictably, these rods and bearings have a high rate of wear and should be checked frequently and replaced as needed.
Old-style guide bearings had grease fittings for regular lubrication. Newer replacement guide bearings lined with a special plastic compound do not require lubrication. The hand-cranked threaded clamp rods of the manual design include threaded blocks with grease fittings that must be lubricated regularly. Excessive wear can cause noise, vibration, inefficient separation, and unwanted movement or loss of sample material from the screen trays. - Drive Systems: A powerful electric motor drives an eccentric shaft mounted on the top of the frame. A connecting rod on each side of the shaft operates through a wrist pin connection and rapidly moves the screen trays up and down to agitate the sample. Grease fittings at the shaft and wrist pin locations require lubrication at recommended intervals. V-belts should be checked often for proper tension and general condition.
Gilson Test-Master® Testing Screens
TM-5 and TM-6 Test-Master have identical sieving actions to standard Testing Screens and include many features that optimize performance and ease of use. The quiet vibration-free operation, minimal dust output, and a tilting hopper for controlled sample feed are all improvements to this version. The Test-Master operating manual provides a complete set of instructions and information.
- Installation: Test-Master models require only a sturdy floor and enough room to open the cabinet doors. The smooth operation of the counter-balanced drive means no permanent bolting is necessary.
- Clamping Systems: A foot-pumped version of the Gilson hydraulic pump activates a hydraulic cylinder assembly operating below the screen trays. The cylinder pushes the trays up to secure them for operation.
- Drive Systems: The electric motor operates a smooth, counter-balanced drive assembly in the base of the unit. A single connecting rod turns an eccentric to provide vertical motion. The screen tray assembly rides up and down on guide pins with brackets. This design serves a similar purpose to the clamp rods of the Testing Screen models but is easier to maintain. The condition and tension of timing and drive belts require periodic checks and occasional adjustment.
Gilson Porta-Screen®
PS-3 and PS-4 Porta-Screens are smaller and lighter, designed for limited applications or temporary locations. Simple design and quiet operation are the main features of these models.
- Installation: Porta-Screens do not require installation beyond leveling and connection to an electrical outlet. They operate in any location from an established laboratory to a temporary construction trailer.
- Clamping Systems: Manual levers mounted on rods rotate down to draw the screen trays together and secure them for operation.
- Drive Systems: Semi-circular weights counterbalance the vertical agitation of the screen trays for smooth and stable operation. Guide pins at the top and bottom of the screening assembly ensure stable agitation.
Gilson Continuous-Flow Screens
CF-1 Continuous-Flow machines feature variable variable-speed drives and tilt-adjustable frames to control material throughput.
- Installation: Continuous Flow Screens require bolting to a concrete floor and proper connection of the wiring of the electronic variable-speed drive.
- Clamping Systems: Threaded clamp rods manually tighten the screen trays for agitation. Grease fittings on the clamp rods allow periodic lubrication.
- Drive Systems: Continuous Flow models feature similar design and construction to the Testing Screen. Connecting rods driven by an eccentric shaft move the screen trays up and down to agitate the sample material. Scheduled lubrication of grease fittings and frequent checking of V-belts for proper tension and general condition ensures optimum performance. The electronic variable-speed controller requires little maintenance.
Gilson-Matic® Screening Assemblies
GX-4A1 and GX-4A2 Gilso-Matics are powerful machines are designed for integration into an automated, total quality control system for testing materials up to 6in (152mm). They can be equipped with or without a hopper and can test total sample volumes up to 10.5ft³ (0.3m³) in batch sizes from 1-3ft³ (0.03-0.08m³).
- Installation: Gilso-Matic screening assemblies can operate as stand-alone units or as part of a custom sampling screening system at a specific plant. Installation may involve simply securing the unit to a concrete floor, or integration into a larger design.
- Clamping Systems: Pneumatic cylinders control clamping, positioning, and discharge of the wire cloth decks and operation of hopper feed gates if equipped. An airline oiler lubricates the cylinders and requires periodic topping off with light oil.
- Drive Systems: The Gilso-Matic has a counterbalanced drive mechanism for smooth operation and requires scheduled lubrication through grease fittings at critical points. Monitoring the condition and tension of drive and timing belts is crucial.
Resources for Maintenance & Repair
There are three valuable resources for maintenance and repair of Gilson testing screens:
- Product Manuals for the various testing screen models contain detailed installation, operating, and maintenance instructions as well as parts lists and diagrams. A manual is provided for each unit shipped, and updated editions are available on our website at the links below:
- TS-1, TS-2, TS-3 Testing Screen
- TS-4 Silent Testing Screen
- TM-5, TM-6 Test-Master®
- PS-3, PS-4 Porta-Screen®
- CF-1 Continuous-Flow Screen
- GX-4A Gilso-Matic® Screening Assemblies
- Maintenance Videos feature Gilson-approved methods for keeping your screening equipment operating smoothly.
- Hydraulic Clamping Systems
- Inspecting the Hydraulic Cylinder Assembly in a Gilson Testing Screen
- Refurbishing the Gilson Testing Screen Hydraulic Pump
- Checking the Oil in a Gilson Testing Screen
- Gilson Testing Screen Do-It-Yourself Hydraulic Pump Replacement
- Testing Screen
- Installing Your Gilson Testing Screen
- Leveling the Gilson Testing Screen
- Checking, Adjusting, or Replacing the V-Belt on a Gilson Testing Screen
- Testing-Master
Gilson’s Technical Support Team has the in-depth product knowledge you would expect from any reputable manufacturer, but we go a step beyond with our deep background of practical experience in materials testing. Contact our testing experts when you need help with any Gilson model, past or present.
Testing Resources
Standard Test Methods, Specifications, and Practices
Individual test methods and specifications referenced in our product descriptions, blog articles, and videos are available for review or purchase from the professional organizations noted.
- ASTM International (American Society for Testing and Materials)
- AASHTO (American Association of State Highway and Transportation Officials)
- ACI (American Concrete Institute)
- State DOTs (Departments of Transportation)
- ISO (International Organization for Standardization)
- BS (British Standards)
- EN (European Standards)