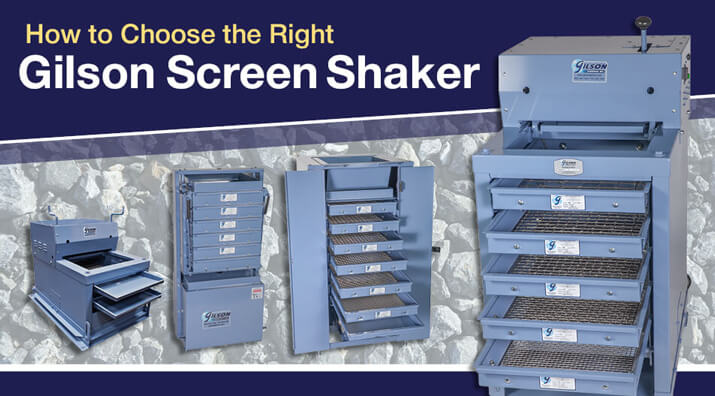
Gradation tests to determine the particle size distribution of fine construction materials aggregates are easy to perform with conventional test sieves. Still, accurate separation of coarse aggregate sizes is always a challenge without the proper equipment. Sample sizes for coarse aggregates must be much larger and heavier to ensure the sample tested represents the whole, making it demanding to perform gradations. These issues are easily solved using Gilson Testing Screens. Our screen shakers perform reliable gradation testing of coarse materials in large quantities. The screen trays have more capacity than conventional sieves, and the frames and drive mechanisms of the machines are much more robust than traditional sieve shakers. For this three-part series focusing on Gilson screen shakers, we’ll guide you on the selection of the best model for your application, maintaining the equipment to ensure a long service life, and finding accessories that enhance testing efficiency in your lab.
We have discussed many times in this blog the importance of particle size and distribution when testing construction aggregates. The particle size distribution curve is a powerful predictor of the properties of asphalt and concrete mixes. Particle size gradations are the most often-performed tests on aggregates, and effective characterization can’t move forward without them. Testing screens offer an efficient and cost-effective method for accurate size determinations of coarse materials.
The Original Testing Screen: Responding to a Need
In the early part of the twentieth century, there was something of a renaissance period around the science of construction materials and their practical application in the built environment. Material scientists were steadily increasing their knowledge of manufactured and natural substances like hydraulic cement, asphalt binders, and soils, finding ways to optimize their properties and behavior. Engineers were quick to take advantage of this newfound knowledge to optimize the design and quality of pavements and structures.
By the 1930s, it was common knowledge that both the size of aggregate particles and their percentage of the whole have a predictable impact on the behavior of concrete and asphalt mixes. Closer control of sizes and proportions meant higher-quality products, more efficient and durable designs, and ultimately, higher profits. For aggregates, the missing link was how to generate accurate and reliable gradations for coarse aggregates.
During this time, an aggregate producer in Pennsylvania was looking for a better way to control the consistency of the product they supplied for highway construction. A plant foreman tasked with finding a new approach fabricated a prototype shaker with vertical agitation that would separate size fractions accurately and repeatably. By 1939, the Gilson Testing Screen was in full production, with steadily rising sales to aggregate producers, testing laboratories, and state departments of transportation (DOTs) nationwide. Of the more than 20,000 Testing Screens produced since then, many manufactured in the mid-1940s are still in regular service.
New Testing Screens for New Applications
Testing Screens based on the original invention are still the workhorse models used every day in labs all over the world. The simple design is easy to operate and maintain and an effective choice for producing accurate and reliable results. Screen Trays for Testing Screen and Test-Master® models are interchangeable.
- TS-1 is the Testing Screen of choice for accurate and efficient testing of large coarse aggregate samples. Five screen trays and a fines collection pan, or dustpan, are held securely in place by Gilson’s unique hydraulic clamping system.
- TS-3 is based directly on the TS-1 design but adds space for an additional screen tray. Having one more tray in a test cycle makes it easier to test samples requiring multiple-size fractions.
- TS-4 addresses the challenge of dust and noise in the lab. This model is a variation of the TS-3 design and includes a sound-damping lid and door to reduce noise and control nuisance dust. Interior surfaces lined with sound-damping material reduce noise propagation. An integrated digital count-down timer controls operation.
Test-Master® models duplicate the vertical agitation action of the original Testing Screen but have a unique drive design that reduces noise and external vibration. This counterbalanced system lets the Test-Master® be operated anywhere in the lab with no need to be bolted to the floor. An integral safety-interlocked cabinet lined with sound-deadening material controls noise and dust, and the built-in sample hopper allows controlled feeding of sample material to the screens during operation. The built-in digital countdown timer precisely controls operation.
- TM-5 Test-Master® holds six screen trays plus a dustpan.
- TM-6 Test-Master® holds seven screen trays plus a dustpan.
Porta-Screen® units feature compact size and simple design for easy transport and set-up in remote lab locations. These models are ideal for smaller test samples with a maximum particle size of 2in (50mm) or so. Like the larger Test-Master units, they have a smooth-operating counterbalanced design for use on any sturdy floor with no permanent mounting. This feature makes them ideal for use in trailers or other temporary project structures. The electronic digital count-down timer ensures accurate test times. Dual hand levers securely clamp the screen trays.
- PS-3 Porta-Screen® holds five screen trays plus a dust pan.
- PS-4 Porta-Screen® holds seven screen trays plus a dust pan.
Continuous-Flow Screen quickly scalps and separates large amounts of materials into one or two size fractions. As materials are fed continuously onto the screens, the exclusive screen trays with chutes are agitated on an incline up to 10° so that separated material flows out for collection in bags or pans. The unit operates with one or two trays, and the agitation frequency is adjustable to optimize the separation of different materials. These models can be used for limited particle size testing if adjusted for level operation. Standard Testing Screen/Test-Master screen trays will fit the Continuous Flow Screen, but have no discharge chute.
Gilso-Matic® Screening Assemblies are large-scale QC/QA systems for aggregate production applications. They are built to process materials with maximum particle sizes of 4in (100mm), or 6in (150mm) and can test single batches of material up to 3ft³ (85L). An optional hopper assembly collects as much as 10.5ft³ (297.3L) of material for batch feeding. The permanently mounted trays have replaceable wire cloth units for sizing. Air-actuated pistons secure the trays during agitation, then tilt and vibrate them afterward to discharge fractions into collection chutes. The custom integration of Gilso-Matic assemblies into a larger system for sampling and testing of aggregate production runs is typical.
Screen Trays and Dustpans are purchased separately for all shaker models. Screen trays for Test-Master® and Testing Screen models are interchangeable. Screen trays are available fitted with ASTM or ISO wire cloth in any opening size, optionally verifiable as Inspection or Calibration grades within these standards. Trays are also available with ASTM E323 perforated plate openings for coal testing and other applications. Specialty Dustpans for unique applications fit Test-Master and Testing Screen models.
We hope this blog post has helped you understand your options when selecting the best testing screen model for your application. Please contact our testing experts to discuss your application.
Testing Resources
Standard Test Methods, Specifications, and Practices
Individual test methods and specifications referenced in our product descriptions, blog articles, and videos are available for review or purchase from the professional organizations noted.
- ASTM International (American Society for Testing and Materials)
- AASHTO (American Association of State Highway and Transportation Officials)
- ACI (American Concrete Institute)
- State DOTs (Departments of Transportation)
- ISO (International Organization for Standardization)
- BS (British Standards)
- EN (European Standards)
Additional Resources
Gilson Videos
- Gilson Testing Screen
- Gilson Test-Master® Testing Screen
- Gilson Porta-Screen®
- Gilso-Matic® Screening Assembly