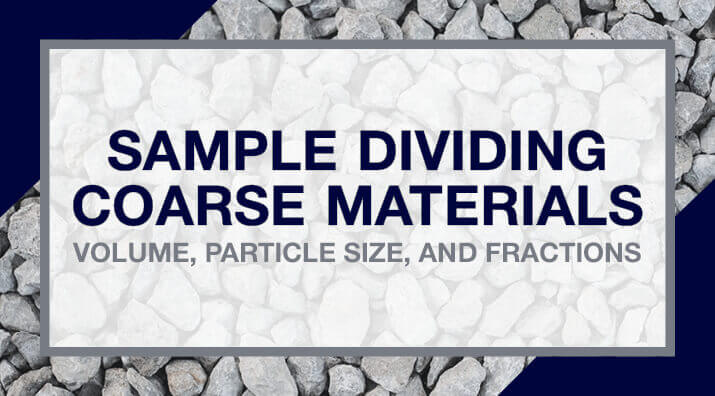
Several articles on this website discuss the importance of proper sample dividing practices and how to select a sample splitter. Most popular sample splitters follow the common theme of dividing a bulk sample of dry granular material into two halves by pouring it over a series of chutes. Sometimes, that’s not good enough. You may need more than two fractions from a single pass, or maybe your bulk sample has unique properties. For this blog post, we’ll take a deep dive into Gilson’s selection of specialty large volume splitters. These are the sample dividers you don’t see every day but have some unique features that could solve a problem for you.
Gilson has always led the way when designing laboratory equipment for dividing dry granular materials. We know typical open-chute splitters aren’t always up to the task of producing accurate representative samples of dry granular materials for laboratory tests. Whether you call these devices sample dividers, splitters, or rifflers, this equipment is built from the ground up to provide the most accurate representative samples possible for your material.
When we discuss material sampling and dividing equipment in our catalog or on our website, we often refer to the chart below. This statistical information illustrates the impact of good sampling practices and makes the point that the selection of both method and equipment is essential.
A. A. Khan investigated the accuracy of various types of sampling at Bradford University in 1968. He based his tests on a 60/40% mixture of coarse and fine sands.
Comparison of Sample Dividing Methods
Capacity, Efficiency, and Versatility
Standard sampling specifications, such as ASTM D75 for aggregates, often require collection of large bulk field samples of 100lb (220kg) or more to produce representative samples for laboratory tests.
Innovative Split-O-Matic Laboratory and Production Splitters take on large volumes of bulk field or production samples and reduce them to 1/2, 1/4, or 1/8 representative fractions in a single pass. These splitters produce final, testing-size sample fractions in fewer passes, with greater accuracy, minimal sample loss, and reduced variability. The Split-O-Matic design divides samples over three or more stages of chutes controlled by positioning of fraction gates.
With capacities for both laboratory and production plant applications, Split-O-Matics have been in production for decades with a design that remains state-of-the-art today. Their effectiveness comes from the particle size and sample capacity of the larger models and their versatility.
- Laboratory Split-O-Matics include gate-release hoppers with capacities up to 3ft³ (85L) for materials with a maximum particle size of 2in (50mm). Front panel doors control dust during operation and open for easy cleaning. These units are ideal for processing sizeable incoming bulk samples quickly. The option to select 1/2, 1/4, or 1/8 sample fractions makes them versatile enough for any sample size.
- Production Split-O-Matics have the same multi-stage design as laboratory models but handle more volume with larger top sizes. Sample materials up to 6in (150mm) can be split accurately into 1/2, 1/4, or 1/8 final fractions in a single pass. Gate-release hoppers are ordered separately in capacities up to 12ft³ (340L). Production models built to customer specifications for permanent installation in production or pilot plant applications can have optional air-actuated controls for hoppers and fraction gates.
Four Samples at Once and No Dust
The Quadri-Splitter meets ASTM D2013 requirements for the preparation of coal samples but is just as useful for reducing mineral aggregate samples according to ASTM C702. The enclosed dust-free design makes this model an excellent choice for ores, coke, and other granular materials as well. When the tilt-feed mechanism is activated, everything from the feed hopper to the sample pans is totally enclosed, so nuisance dust can’t escape. The maximum particle size for mineral aggregates is 1/2in (12.5mm), and feed pan volume is 0.7ft³ (20L). One pass yields four representative 1/4 samples, and a second pass provides four 1/16 samples.
Safe and Efficient Handling of
Asphalt and Aggregates
Asphalt paving materials sampled at point-of-placement are large, heavy, and very hot. The design of Gilson’s Quartermaster is a safe and efficient approach to splitting bulk samples of hot asphalt material and a practical way to split large aggregate and soil samples as well. The simple two-piece design is portable for easy transport and set up at the sampling site. The operator has complete control when releasing 120lb (55kg) or more of material from the large hopper to the divider below. Divided fractions can be routed directly into Bucket Liner Sample Bags, minimizing handling and contact with hot materials. Four separated fractions are bagged at once, ready for immediate transport to the lab.
Small Fractions from Large Volumes
1/16 Sample Reducers (or table samplers) use upright dividers on a steeply inclined table surface to form a system of chutes and openings to obtain a small fraction in one pass. Material cascades down from the hopper-feeder to be evenly separated as it flows through the separate chutes. Reject material falls through multiple openings into a waste receptacle, leaving a single 1/16 representative fraction in a separate container for testing.
- 1/16 Sample Reducer features a cast aluminum flow table and 0.25ft³ (7.1L) hopper with an adjustable sliding gate.
- Gilson Heavy Duty 1/16 Sample Reducer features a large 1.0ft³ (28L) hopper with an adjustable sliding gate. The Reducer splits samples of 100lb (45kg) or more in a single batch or feeds larger bulk samples continuously. All-steel construction meets the requirements of ISO 13503-2:2006 and API STD 19C.
Heavy Duty Construction for Long Life
The Gilson California Splitter features heavy-duty construction and is an ideal choice for demanding use in busy labs. Built to a California Department of Transportation (Caltrans) design for sample preparation of aggregate samples; it meets ASTM C702, California Test 201, and AASHTO T248 requirements. The rugged fixed-chute riffle splitter has a 1.9ft³ (53.8L) gate-release hopper and ten chutes to produce accurate splits of mineral aggregate material up to 1.125in (28.6mm). Heavy-gauge welded steel construction throughout stands up to continuous use, and swivel casters allow easy mobility. Models are available with lighter aluminum sample pans for easier handling of divided fractions.
We hope this blog post has provided some guidance on equipment selection.