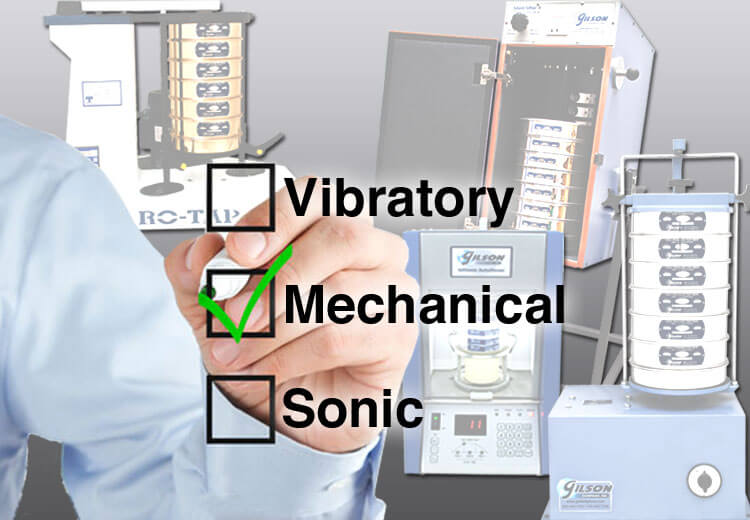
Particle Size Analysis by Sieving
Sieving is a method of separating and classifying granular materials that dates back to ancient times. Today, sieve analysis is used by scientists, civil engineers, and others to determine particle size distribution for many materials to meet QC/QA requirements. Hand sieving is the most basic way to perform sieve analyses and is acceptable for applications where a high degree of efficiency, accuracy, and repeatability are not essential. Results are highly operator-dependent and can vary significantly. Hand sieving tests can also only be performed on one sieve at a time.
What is a Sieve Shaker?
Sieve shakers automate the agitation of particles in a sample for separation and size determination. The appropriate sieve shaker agitation method is determined by the particle size, minimum size to be separated, wet or dry sieving, and sample characteristics such as resistance to agglomeration and static electric factors.
Wet-sieving accessories are available to supply and drain away wash water from the sieve stack. Specialized wet-sieving shakers are also available. These vibratory sieve shakers feature systems for pumping and recycling wash water, along with vacuum systems to increase material throughput.
Advantages of a Sieve Shaker:
- Saves considerable amounts of testing time
- Automates particle agitation
- Improves accuracy and repeatability of fraction separations
Selecting a Sieve Shaker
The right sieve shaker will have a significant effect on your sieving results and test times. Particles react differently to different mechanical actions. It’s also important to consider factors including agglomeration, static attraction, desired sample volume, the noise level during operation, and degradation. With all of these factors to consider, how do you know which machine is most suitable for your purposes? Follow our guide for answers to your questions.
3 main types of Sieve Shakers
Mechanical Sieve Shakers
Mechanical Sieve Shakers have motor-driven mechanisms to agitate and reorient particles with orbital, circular, or rotational motions. Mechanical Shakers are the most economical choice.
Some mechanical shakers also use repetitive tapping of the sieve stack to further reorient particles, aid passage of near-size fines, and prevent blinding and dead spots on the mesh surface. The mechanical tapping motion improves the passage of nearly any material while assuring accurate and consistent results. Non-Tapping Mechanical Sieve Shakers are often more affordable and may be sufficient for free-flowing materials that are easily sieved and coarser than #200 (75µm).
When should I use a mechanical sieve shaker?
Use a Tapping Mechanical Sieve Shaker when you’re looking for the sharpest separation of materials from 2in (50mm) to as fine as No.635 (20µm). These models work well for a wide range of materials, especially those with a higher percentage of fines. The mechanism and tapping action combined with the agitation of particles can make noise a significant concern in the lab. Some models are now available enclosed in sound-deadening cabinets and using noise reduction technology to mitigate this issue and protect workers.
Vibratory Sieve Shakers
Vibratory Sieve Shakers use quiet electromagnetic energy to agitate particles. A proper vibration setting creates a fluid-like, moving bed of the sample material, evenly distributing material across the mesh as it lifts and reorients particles to ensure the maximum number of passing opportunities. A Vibratory Sieve Shaker can accommodate a wide range of materials and adjustments can be made for vibration amplitude and frequency. A programmable “pause” feature can have an effect similar to tapping in helping fines pass while preventing blinding. These compact units yield fast, accurate results and some even allow the user complete control to select the vibration level based on material type.
When should I use a vibratory sieve shaker?
Use a Vibratory Sieve Shaker for materials between 1in (25mm) and No. 635 (20 µm). It’s ideal for granular and fine materials, especially pharmaceuticals, dry powders, cosmetics, and foods. The range of energy input possible on many units makes them useful for materials that may not readily separate from other shakers. The quieter actions of vibratory shakers often make them a better choice where excessive noise can be a factor.
Sonic Sieve Shakers
Sonic Sieve Shakers use up 3,600 sonic energy pulses per minute from an audio generator, creating an oscillating air column enclosed by the sieve stack. The continuous agitation excites the particles and continuously reorients them to the mesh surfaces. All Gilson Sonic Sievers have high-quality variable and programmable power input and both horizontal and vertical tapping.
When should I use a sonic sieve shaker?
Sonic Sieve Shakers are often used to perform precision separations on small volume and particle size specimens as fine as 3 µm, making these shakers especially effective for powders, fine granular materials, and “problem” materials. There are different models available for use with 3in (76mm) or 8in (203mm) diameter sieves depending on the desired sample volume. The 3in (76mm) sieve shaker uses woven wire or precision electroformed cloth with acrylic frames, while the 8in (203mm) sieve shaker uses standard metal frame sieves with woven-wire or precision electroformed cloth.
Selecting the proper sieve shaker can be a challenging process, and it’s important to understand that not all sieve shakers are the same. Our video below further explores the features and capabilities of the various shakers available.
Click the Sieve Shaker Comparison Table below to enlarge, print, or download to compare all Gilson Sieve Shakers.
We hope this blog has been informative and has given you some tips on which type of shaker best suits your needs.