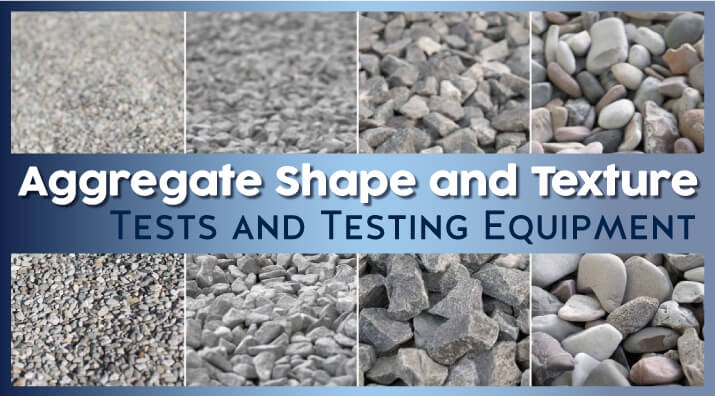
The effects of the particle size and gradation of construction aggregates used in asphalt or concrete aggregates, or on their own as compacted base materials, are widely known, but particle shape makes a difference. The shape, aspect ratio, and texture of construction aggregates significantly influence the performance of the finished product.
Construction aggregates are traditionally mined or extracted from natural sand and gravel deposits or geological rock formations, then further crushed and sorted into size fractions for blending. Aggregates derived from by-products of iron and steel production (slag) or produced from recycled concrete are increasingly popular as access to natural sources becomes more restrictive and expensive. Fine and coarse aggregates make up 90 to 95 percent of the volume of asphalt and 70 to 80 percent of the volume of concrete mixtures.
The characterization of aggregate shape properties can make the difference between poor performance in roads and structures or long useful service life. In just a few examples:
- Sharp, angular aggregate shapes and textures add strength to hardened concrete but increase the water demand during batching to maintain workability during placement. More cement is required to maintain a water/cementitious (w/cm) ratio that ensures adequate strength with the increase in water volume. Asphalt mixes become more difficult to compact to specified void ratios.
- Aggregates with rounded shapes produce fresh concrete that flows into confined spaces more easily during placement, but modification to the mix design is required to control segregation and promote strength development. Asphalt mixes with rounded aggregates are difficult to compact correctly and tend to shove or rut over time.
- Flat and elongated aggregate particles can lock together to hamper the compaction of asphalt pavement mixtures and make the mix unstable if a significant number of particles fracture. Concrete mixes with these particles are difficult to place, resist consolidation, and are hard work to finish. Flat particles in concrete may trap bleed water after consolidation, creating pockets of low strength.
Some visual classifications of aggregate particle shapes and textures use terms like angular, sub-angular, sub-rounded, and rounded. Other words include irregular or flaky. The terms flat and elongated most often refer specifically to ratios of dimensions measured with proportional calipers, gauges, or templates.
There are some standard laboratory test methods to classify and quantify shape and texture characteristics. Although there is ongoing research and proposed methods for using digital imaging systems to measure aggregate shape properties, automated procedures have not gained widespread acceptance in specifications in this writing.
ASTM D4791 Flat and Elongated Particles
ASTM D4791 test method compares the dimensions of individual coarse aggregate particles. Specimens of approximately 100 particles from each size fraction are manually measured with a proportional caliper to determine the width, length, and thickness ratios.
- A flat particle has a ratio of width to thickness greater than a specified value.
- An elongated particle has a ratio of length to width more than a specified value.
- A flat and elongated particle has a ratio of length to thickness greater than a specified value.
Flat and elongated particles fracture easily under load and are difficult to compact in asphalt paving mixtures. Fractured particles also negatively affect void content, stability, and binder distribution in asphalt and negatively affect the workability and consolidation of fresh concrete.
BS EN 933-3 Flakiness Index and Elongation Index
British and European standards define aggregate proportions by flakiness and elongation measurements. The Flakiness index is the percentage by weight of particles with a thickness less than 0.6 times their mean particle dimension. Particles are classified as elongated when the longest dimension is more than 1.8 times the nominal opening of the sieve fraction. Many state DOTs have adopted BS EN 933-3, a popular test for aggregate classification.
Coarse aggregate particles with nominal sizes from 6.3 to 63mm (0.25 to 2.5in) are sorted into size fractions and sampled for manual manipulation through flakiness and elongation gauges.
- Flakiness gauge is a flat metal piece with cut-outs to measure particle thicknesses for size fractions.
- Elongation gauge consists of six upright pins fixed on a flat metal base to measure the maximum length of particles in each size fraction.
ASTM C1252 & AASHTO T 304 Fine Aggregate Angularity
Fine Aggregate Angularity tests measure the uncompacted void content of fine aggregates and indirectly characterize their particle shape and surface texture. Higher void content indicates greater angularity and roughness of the particles. Good angularity and texture of fine aggregate particles increase the strength of paving mixtures. Rounded aggregate can result in pavements prone to rutting and shoving under traffic loads. If the aggregate is too rounded, the shear strength of the matrix is reduced.
The ASTM C1252 and AASHTO T 304 test procedures are performed using the uncomplicated fine aggregate angularity apparatus and are simple to perform. A prepared sample of fine aggregate is allowed to flow freely from the funnel-shaped hopper of the device and into a calibrated cylindrical measure. The mass of the retained sample, the volume of the cylinder, and the specific gravity of the material are used to calculate the uncompacted void content. Different methods within the standard cover testing of graded samples or individual fractions.
AASHTO T 326 Coarse Aggregate Angularity
AASHTO T 326 Coarse Aggregate Angularity tests use the same procedure as the fine aggregate angularity test to determine the uncompacted void content of coarse aggregate. The coarse aggregate angularity apparatus is scaled up in size to accommodate the larger aggregate particles. There are two procedures to test combined graded aggregates and one to test individual size fractions. ASTM does not currently list a procedure for this test.
ASTM D5821 Fractured Particles in Coarse Aggregate
ASTM D5821 test method establishes the percentage of particles with fractured faces in a coarse aggregate sample and satisfies specification requirements for percentages of fractured particles. Fractured particles maximize shear strength in unbound and bound aggregate mixtures and provide stability in asphalt pavements. The test is a visual examination and manual sorting of coarse particles in an aggregate sample, and results can be reported as percentages of total mass or by particle count. Testing equipment is minimal, consisting of a mechanical sample splitter, ASTM E11 test sieves, laboratory balances with required capacity and sensitivity, and a lab spatula.
Flatness and Elongation in Rail Ballast Aggregates
Aggregate used for rail ballast can break down and create an unstable rail bed if there is an excessive proportion of flat and elongated particles. These simple aggregate size templates were developed by the Tokaido Shinkansen railway in Japan and are under review for applications in the US.
We hope this blog post has informed you of the various test methods and equipment used to characterize aggregate particle shape and texture.