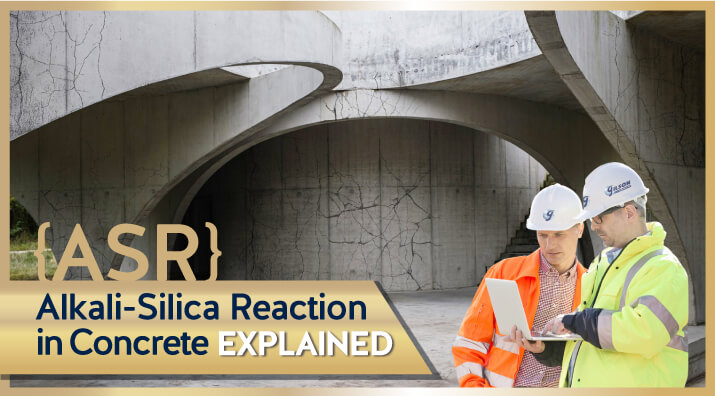
Although Alkali-Silica Reactivity (ASR) has created problems in concrete mixtures for centuries, the mechanism was not understood and documented until the mid-1930s. Thomas Stanton, an engineer with the California State Division of Highways, identified the issue. By 1940, he had completed his research showing that alkali content in cement, the amount of reactive silica in the aggregate, and the availability of moisture caused the expansion of sample mortar bars in laboratory tests. ASR is now recognized as a significant cause of concrete deterioration anywhere in the world where siliceous aggregates are found.
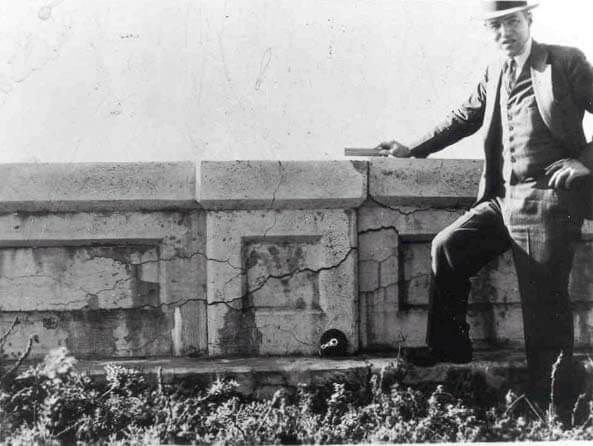
What is ASR in Concrete?
Alkali-Silica Reactivity (ASR) is a chemical reaction between alkalis in the cement fraction of concrete mortar and certain types of siliceous aggregates. Resulting in the expansion and cracking of the concrete.
There are at least two types of interactions between cement components and aggregates that cause similar damages from expansion and cracking. The umbrella term of Alkali-Aggregate Reaction (AAR) describes both of these conditions.
- ACR (Alkali-Carbonate Reaction) is a reaction between alkalis in the concrete mortar and the chemical components of carbonate rocks like dolomitic limestones. The reaction causes crystallization and considerable expansion, resulting in substantial damage in a short amount of time. ACR does not respond to mitigation efforts, so the best solution is the avoidance of these aggregates. Fortunately, these aggregates are usually recognized as unsuitable for use, so ACR issues in hardened concrete are relatively rare.
- ASR (Alkali-Silica Reaction) is a reaction driven by a combination of reactive aggregates, high (alkaline) pH values, and water. A type of gel material forms at the interface between the aggregate particles and the cement mortar. This gel is highly expansive in the presence of water. The reaction process may take years, but once the reaction is underway, the forces from expansion cause cracking to appear on the surface. This blog post will focus on ASR and tests to detect the potential in aggregates and aggregate-mortar mixes.
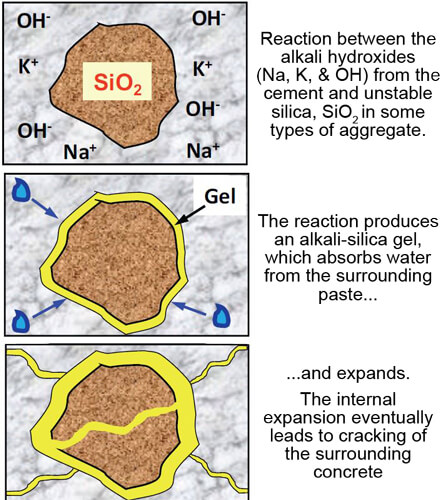
- Photo Credit:
The Effect of Alkali-Silica Reaction on Concrete
The initial expansion and cracking of the concrete may not be severe enough to compromise the integrity of the structure. However, ASR cracking provides a pathway below the surface for water and chemicals to initiate freeze-thaw damage cycles and promote the corrosion of reinforcing steel. The effects of ASR eventually shortens the useful service life of the structure and does extensive cosmetic damage as well. Millions of dollars are lost annually to the cost of repairs or replacement of concrete roads, bridges, and structures.
Symptoms of Alkali-Silica Reactivity
Evidence of ASR activity can take years to appear in hardened concrete. Irregular surface cracking with gel material, sometimes seeping from the cracks, is often the first outward sign of trouble. Confirmation of ASR activity in existing concrete is better than not detecting it at all. Damaged sections can be repaired, and ingress of water slowed, but the process may continue. Detection, testing, and diagnosis of ASR do have value in the documentation of an undesirable source of aggregate materials or unsuccessful mix design. Gilson’s ASR Detect Kit uses reagents to detect initial or advanced stages of ASR by color staining following a reaction. The test is completed in less than five minutes, and the reaction stains are permanent.
Alkali-Silica Reaction Prevention
Fortunately, there is a growing field of knowledge of potential reactions between cementitious materials and aggregate types. The causes are well understood, and adequate testing can help predict and avoid or at least mitigate, ASR before concrete production. Testing reveals the presence of ASR-sensitive materials, and strategies like control of moisture, modification of cementitious materials content, and the use of admixtures reduce the potential severity of the reaction.
Avoiding problems caused by ASR does not have to be complicated. The Federal Highway Administration (FHWA) recommends the logical first step of examining the field performance history of the aggregate source.
- Have existing concrete structures using the same aggregate source and similar concrete mixtures exhibited ASR problems?
- If the aggregates have already been tested and exhibited ASR potential, what were the mitigation methods used: Lowering the alkali profile? Controlling permeability of the concrete? Reducing pH with admixtures?
Judging aggregate quality using these methods can save time and expense but may be difficult to verify. Documentation may be incomplete, or information on materials may be considered proprietary by previous users.
The Portland Cement Association has published this flow chart to guide users in assessing aggregates for concrete.
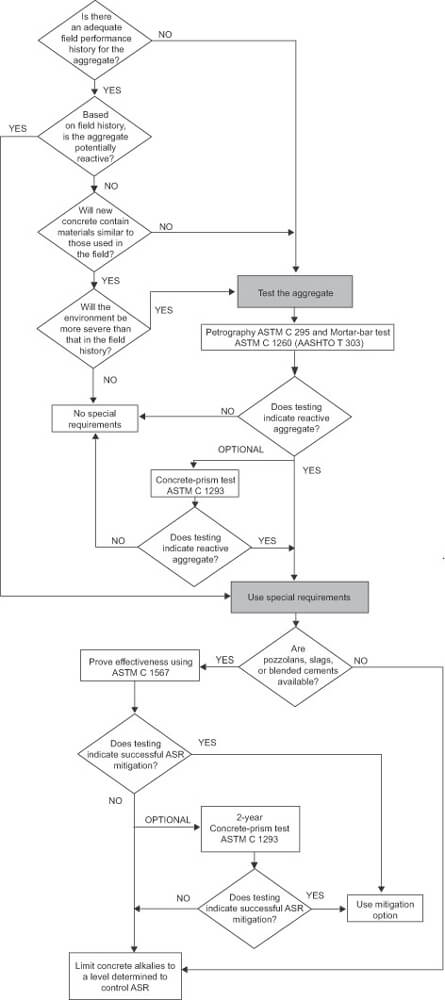
As the chart shows, finding that a supply of aggregates is reactive is not necessarily the end of the line. Certain types of fly ash, blast furnace slag, or other supplementary cementitious materials (SCMs) substituted for Portland cement in the mix design may mitigate the onset of ASR. Decreasing the permeability of the concrete using proper mix design and placement techniques will also help by reducing the amount of water penetrating the surface.
Additions or modifications can be made to the cementitious materials to reduce or eliminate the severity of the reaction.
Which Tests Identify Reactive Aggregates?
Most tests to determine ASR potential use similar equipment and procedures and are performed before the design, approval, and placement of concrete mixes. Laboratory mixes are prepared in laboratory mixers using fine aggregates, cement, and sometimes additional SCMs
- ASTM C490/AASHTO R 70, Use of Apparatus for the Determination of Length Change of Hardened Cement Paste, Mortar, and Concrete, outlines the equipment and general procedures for measuring length changes in cement and concrete specimens. The apparatus noted in this practice is referred to in all the length-change ASR tests.
- ASTM C1293, Determination of Length Change of Concrete Due to Alkali-Silica Reaction, is known as the concrete prism test (CPT) and is considered the best test for assessing aggregate performance. The total test procedure has a duration of one to two years, making it impractical for many applications.
- ASTM C1260/AASHTO T 303, Potential Alkali Reactivity of Aggregates (Mortar-Bar Method) identifies aggregates that are reactive when exposed to the alkalis in cement paste. Standard Portland cement is used to prepare the samples. The test is completed in 16 days, making it more useful for short-term screening of aggregate sources.
- ASTM C1567, Determining the Potential Alkali-Silica Reactivity of Combinations of Cementitious Materials and Aggregate (Accelerated Mortar-Bar Method), identifies mix designs that will mitigate the effects of reactive aggregates. Various blends of Portland cement, SCMs, and aggregates are combined with reactive aggregates to determine expansive properties. The complete test cycle takes 16 days.
- AASHTO T 380 Potential Alkali Reactivity of Aggregates and Effectiveness of ASR Mitigation Measures (Miniature Concrete Prism Test, MCPT) is a newer test that combines elements of the ASTM C1293 and C1260 tests. The intent is to produce results as accurate as C1293 in a much shorter timeframe. Some state DOTs consider the test method to be promising. The test cycle for this method requires 8 to 12 weeks instead of 1 to 2 years.
All these tests require consolidating prepared mortar samples into molds to produce a rectangular bar or prism. Stainless steel gauge studs installed in the molds remain embedded in the concrete prism for periodic length measurements. After a brief period of curing and an initial length reading in a length comparator, the specimens are immersed in a heated solution of sodium hydroxide. Periodic length readings detect the expansion of the specimens. Total test time depends upon the test method but may range from 14 days to a year or more.
What Testing Equipment Do I Need?
The samples and procedures for most alkali-silica reactivity lab testing are similar, so the same laboratory equipment is used for many test methods.
- Laboratory Mixer mixes the ingredients for molding length-change prism specimens. The compact benchtop mixer with 5qt (4.7L) capacity meets the requirements of ASTM C305 and multiple ASTM and AASHTO test methods when fitted with the clearance adjustment bracket.
- The Clearance Adjustment Bracket provided on laboratory mixer models that meet ASTM C305 standards is also available separately to modify standard laboratory mixers to meet the specification.
- Prism Molds to form length change specimens are machined from corrosion-resistant steel or stainless steel. Available models form 10in (254mm) long prisms with 1in, 2in, or 3in (25mm, 51mm, or 76mm) square cross-sections. Mold pieces are drilled and threaded to accept gauge studs for precision measurements.
- Prism Gauge Studs ensure precise length change measurements of cement and mortar specimens. The knurled and threaded studs are 316 stainless steel and meet test method specifications. The studs are held in place in the prism molds and embedded when casting the samples.
- Length Comparator measures length changes in mortar bar samples. The comparator meets ASTM and AASHTO test method requirements. Models are available with either analog or digital indicators and are supplied with an alloy steel reference bar to verify comparator measurements.
- A Straight-Edged Trowel is convenient for handling and placing cement and mortar material during molding and is required to strike off sample material in the molds. The trowel complies with ASTM C109 requirements.
- Hard Rubber Tamper is used in several ASTM and AASHTO test methods to consolidate cement and mortar samples in molds.
Learn More About Alkali-Silica Reactivity
ASTM C1778, Standard Guide for Reducing the Risk of Deleterious Alkali-Aggregate Reaction in Concrete and AASHTO R 80, Determining the Reactivity of Concrete Aggregates and Selecting Appropriate Measures for Preventing Deleterious Expansion in New Concrete Construction describes preventative measures, risk evaluation strategies, and recommended laboratory tests for mitigation of ASR in concrete mixes.
The Federal Highway Administration (FHWA) has a comprehensive ASR Reference Center, and past issues of Reactive Solutions, a former quarterly newsletter, follow the research and technical updates on Alkali-Silica Reactivity.
We hope this blog post has helped you understand alkali-silica reactivity in concrete. Please contact our testing experts to discuss your specific applications.
Testing Resources
Standard Test Methods, Specifications, and Practices
Individual test methods and specifications referenced in our product descriptions, blog articles, and videos are available for review or purchase from the professional organizations noted.
- ASTM International (American Society for Testing and Materials)
- AASHTO (American Association of State Highway and Transportation Officials)
- ACI (American Concrete Institute)
- State DOTs (Departments of Transportation)
- ISO (International Organization for Standardization)
- BS (British Standards)
- EN (European Standards)