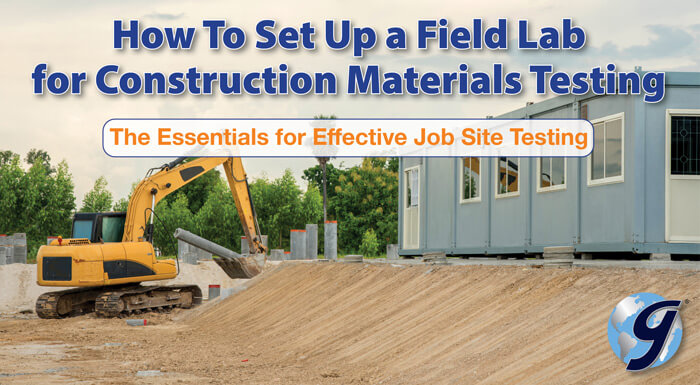
Establishing a field laboratory for construction materials testing is sometimes specified in the contract documents of large projects. Launching a remote lab is a significant undertaking, but even if not mandatory, it can solve some logistical problems.
Benefits Of A Field Lab
Transporting bulk samples or test specimens to a central lab is costly, time-consuming, and risks loss of the materials or damage to specimens. There may be time constraints for performing specified tests and reporting results. The sheer number of tests required on a single project may be overwhelming for a central lab when added to its daily workload.
This blog article will discuss setting up and furnishing temporary field-testing labs with essential laboratory equipment. Field labs are generally limited to a few particular tests, but no matter the material, most require the same essentials to measure properties like size, weight, and moisture. Stay tuned, and we will discuss in next month's blog selecting equipment for specific methods of testing concrete, soils, asphalt, and aggregates in a remote setting.
Planning
Most central construction materials labs begin with a few necessary items, accumulating more equipment over the years as needs arise. When you have to outfit a testing lab from scratch quickly, you’ll need to think differently. If the requirements are straightforward and only for a short time frame, you may be able to reassign some existing equipment from the main facility. But some planning will ensure success for the launch of a well-equipped remote lab.
Laboratory Space
Before selecting equipment, consider the space available, the expected workload and output, and the number of people needed to staff it. Knowing this allows planning to move forward based on equipment footprints, ergonomics, and test method requirements. Manufacturers can provide dimensions and operational space requirements for individual devices.
“Field lab” could mean different things. It might be your self-contained mobile facility for a quick relocation to any project site or borrowed space in a construction trailer or temporary building. Any room should have heating, cooling, and ventilation features and be a safe area for your staff to occupy. You may not have many options here. It could be more a question of what will fit into the space available rather than how much room you would like to have. If the square footage is tight, you’ll need to prioritize, starting with big-footprint equipment that is essential to the lab's function. A testing screen or concrete compression machine demands a lot of space, not just for the unit but for the operating area required around it. Sturdy wall shelving will conveniently position smaller lab equipment like balances, vacuum pumps, and even laboratory ovens.
Utilities
Electrical or plumbing resources at your mobile lab site may be limited or non-existent, and you may need to plan for a generator or temporary water supply.
Creating Your Construction Laboratory Equipment List
The Essentials
There is some equipment that every construction materials testing lab is likely to need. Along with specification compliance and quality considerations, size, weight, power requirements, and cost influence the optimum choices for field applications.
Sieving and Screening: Gradations and particle sizing are core applications for most labs, and for some field labs, maybe their entire purpose. Meaningful quality control testing depends on the accuracy of gradations, so resist the temptation to use second-hand or worn-out sieves and sieve shakers for field applications.
- Test Sieves with 8in or 12in frames depending on expected sample volumes and particle sizes. For storage, you can nest test sieves, but it’s crucial to protect the wire cloth from damage.
- Sieve Shakers require space and electrical power but decisively eliminate the variables affecting manual sieving accuracy. Select models based on test sieve sizes, efficiency, noise suppression, or dust control.
- Screen Shakers are a must for effective gradations of large samples with particle sizes from 4.75mm to 100mm (No. 4 to 4in) or more. Their weight and aggressive mechanical action make sturdy floors necessary if used in temporary structures.
Sample Dividing: Any laboratory handling construction aggregates, soils, or asphalt needs sample dividing equipment to use representative sampling techniques to reduce bulk field materials to representative samples for testing. For field operations, the best choices for sample splitters are those that can adapt to a variety of sample volumes and particle sizes for ASTM C702 and AASHTO R 76.
- Universal Sample Splitters in models with several volume capacities have adjustable width chute bars for the best performance over a wide range of particle sizes.
- Sample Quartering is still permissible in some test methods, but it can be challenging to produce reliably representative samples with this method.
- 1/16 Sample Reducers cut a 1/16 fraction representative sample from free-flowing granular materials in one pass. They are well-suited for fast field sampling of frac sand materials (hydraulic fracturing proppants).
Scales/Balances: Nearly every test method entails a weight determination at some point, so a balance is necessary. A full-size lab may have several scales/balances with various capacities and sensitivities. Still, space and cost concerns may not permit that in a small or temporary lab. One or two suitable units could replace several older models. Back in the day, the remote operation usually meant mechanical scales, but newer electronic models now have a clear advantage. A Digital model with a large capacity, high resolution, and compact size tends to be the most popular. Choose weight capacity and sensitivity based on test method criteria, and ensure the weighing platform is large enough for all applications.
- Digital Lab Scales and Balances are accurate and compact, operate on long-lasting batteries, and are robust. Include secondary features like battery operation, data storage, or detachable displays based on how well they optimize your operations.
- Mechanical Balances and Scales are reliable and do not require a power source. They are also sensitive to movement and air drafts and require frequent calibration checks when relocated.
Ovens: Moisture determinations are fundamental in construction materials testing, especially for soils and aggregates. Laboratory ovens for any application must meet essential sample capacity and temperature range needs. Ovens that are best for field operations include features different from most laboratory ovens. Two restrictions that impact the selection of field models are space and electrical requirements. Drying ovens for field applications must balance sample capacity against available bench space. Power supplies with high voltage or amperage may not be available at satellite locations.
- Laboratory Ovens have the most efficient footprint-to-volume capacity ratio, and most have models to operate on standard 115V/60Hz electrical power. Available floor stands position units at the correct ergonomic height.
- Open-Burner Hot Plates are an option to extend the sample drying capacity for some materials.
Thermometers: There are so many configurations for temperature devices that you’re sure to find many options to meet your needs for range, accuracy, and resolution specifications. As a rule, it is wise to avoid Mercury instruments unless test methods specify them. A broken Mercury thermometer presents an immediate safety concern and causes delays with cleaning up while complying with regulatory requirements. Fortunately, accurate, reliable, and Mercury-free thermometers are widely available.
- Digital Thermometers are safe, accurate, reliable, and rugged. They are available in many models and are a natural fit for remote or field operations.
- Data Logging Thermometers offer the ability to record, timestamp, and store temperature data automatically for sample materials and testing environments.
- General Lab Thermometers and ASTM Thermometers require care in handling and use but are otherwise reliable and not susceptible to problems like drift and the need for frequent calibration.
- Bi-Metallic Dial Thermometers may not feature precision accuracy but are inexpensive and do not require much maintenance aside from frequent calibration checks. If permissible in the test method, they can be a cost-effective choice.
Labware: There are many options for measuring liquid volumes in the lab. It comes down to the amount to be measured and the precision required. Glass provides more accurate and reliable volume measurements. Still, plastic labware can be a cost-effective option to avoid breakage if reduced tolerances are acceptable.
- Beakers are convenient for ordinary measuring and mixing of medium to large volumes of liquid.
- Volumetric Flasks usually have only one graduation at their specified capacity. They are required in several standard test methods and often double as specific gravity pycnometers.
- Graduated Cylinders are an accurate method for measuring and dispensing small to medium volumes of liquids.
- Measuring Pipettes dispense exact, small amounts of liquids. They are not common in construction materials testing but are specified occasionally.
- Sample Containers are all the necessities for handling, transferring, and storing material samples in the lab.
- Sample Bags are popular for handling bulk field samples.
- Metal Sample Pans and Glass Dishes are used for managing samples for preparation and oven-drying. And also useful for handling, transferring, and storing samples for later use in the lab.
- Sample Scoops for handling granular samples.
- Lab Brushes are part of cleaning and maintenance.
- Lab Safety Equipment like eye and hearing protection and gloves is necessary for personnel protection.
- Lab Timers are programmed with the desired time interval and operate until they reach zero and shut off or trigger an alarm. Some models have electrical receptacles to control testing screens, ovens, and other devices. Benchtop Timers operate independently to count up elapsed time or count down to zero. Some have multiple channels.
Measurement: Construction materials laboratories must have a variety of instruments to measure dimensional characteristics for samples and tests. Calipers, measuring tapes, and diameter tapes have unique applications in standard test methods.
- Measuring Tapes are indispensable and have many applications in the lab or field. Models with combined inch and metric units of measure ensure you won’t need to have two different types available.
- Digital Calipers are necessary for precise measurements with a resolution of 0.0005in or 0.01mm. Digital calipers with a 12in or 300mm full range are a bit more expensive than ordinary 6in/150mm models but valuable for many more applications. Most digital calipers are switchable between inch and metric units of measure.
- Pi Tape Measure® offers fast and accurate analog measurements of diameters by merely wrapping the tape around a cylindrical sample.
We hope this blog post has helped you make some decisions about starting and equipping a remote field lab with essential equipment. Follow the links in the article for detailed information and specifications on testing equipment for your field lab. Visit our video library to see Gilson products in action!